Digging Deeper on Tesla's Etherloop Wiring System
发布时间 2024-06-26 14:00:38 来源
摘要
Time for a deep dive on Tesla's EtherLoop, which is the final critical innovation needed for the unboxed manufacturing process.
GPT-4正在为你翻译摘要中......
中英文字稿 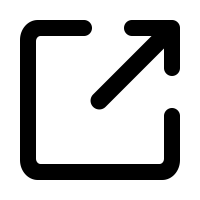
Welcome back everyone, I'm Jordan Geesege and this is The Limiting Factor. Last year at Investor Day, Tesla said the next generation vehicle would use a 48 volt architecture and an ethernet network that would eliminate cross-car wiring, which they later revealed was called Etherloop. The 48 volt architecture understandably attracted more attention and for good reason. The benefit of 48 volts is obvious, which is that quadrupling voltage from a conventional 12 volt architecture allows for 75% of the copper wiring to be removed from the vehicle. However, I'd argue that although the benefits of Etherloop are more abstract, it's an innovation that's more revolutionary than the switch to 48 volts, and therefore worth a deep dive.
欢迎大家回来,我是乔丹·吉瑟吉,这是【限制因素】节目。去年在投资者日活动上,特斯拉宣布下一代车辆将采用48伏电气架构和一个以太网网络,这个网络可以消除传统的车内布线,他们后来将其命名为Etherloop。48伏电气架构显然吸引了更多关注,而且也是有原因的。48伏电气架构的好处显而易见,它将传统的12伏电压提高到四倍,这可以减少车辆中75%的铜线用量。然而,我认为尽管Etherloop的优点更为抽象,但这项创新比转换到48伏更具革命性,因此值得我们深入探讨。
So today, I'll walk you through my best guess at exactly what Etherloop is, why it's such a departure from CAN bus technology that's typically used in vehicles, and why I think it's the key innovation necessary to make Tesla's next generation vehicle a reality. Before we begin, a special thanks to my Patreon supporters, YouTube members and Twitter subscribers, as well as RebellionAir.com. They specialize in helping investors manage concentrated positions. RebellionAir can help with covered calls, risk management, and creating a money master plan from your financial first principles.
所以今天,我会向大家详细介绍一下我对Etherloop的最佳猜想,它到底是什么,为什么它与汽车中通常使用的CAN总线技术有如此大的不同,以及为什么我认为它是实现特斯拉下一代车辆的关键创新。在开始之前,特别感谢我的Patreon支持者、YouTube会员和Twitter订阅者,以及RebellionAir.com。他们专门帮助投资者管理集中头寸,提供备兑看涨期权、风险管理,以及依据您的财务原则制定资金管理计划。
To kick things off, we first need to cover the primary parts of conventional automotive electrical systems. For the purposes of this video, there are three major parts. The first is of course the wiring, which is typically standard copper wire of different thicknesses depending on how much power is required, or whether it's just carrying data rather than power. The second is the endpoints that the wires ultimately feed electricity and data to and from, such as the brakes and the infotainment system. The third part of the electrical system is controllers, which are devices that manage collections of endpoints in the vehicle.
开始之前,我们首先需要介绍一下传统汽车电气系统的主要部分。对于本视频的目的,总共有三个主要部分。首先当然是电线,通常是根据所需的功率或者是传输数据的需求而使用不同厚度的标准铜线。第二个部分是用电和传输数据的终端,比如刹车系统和信息娱乐系统。第三个部分是控制器,这些设备管理车辆中的多个终端。
A typical vehicle has around 70 specialized controllers scattered throughout the vehicle to manage every switch, actuator, and gauge. Some of those controllers will have to manage endpoints spread across the vehicle. For example, a vehicle with traction control might coordinate traction through a central controller that's wired to sensors at each wheel. The fourth part of the electrical system is the communication network that ties together and is made up of the wires, endpoints, and controllers. For the last 40 years or so, vehicles have used a network architecture called CAN, which stands for Controller Area Network, which involves a hardware standard and a communication protocol.
一辆典型的汽车大约有70个分散在各处的专门控制器,用于管理汽车内的每个开关、执行器和仪表。这些控制器中有些需要管理分布在整个车辆上的终端设备。例如,一辆带有牵引力控制的汽车可能通过连接到每个车轮传感器的中央控制器来协调牵引力。电气系统的第四部分是将这些组件连接在一起的通信网络,由电线、终端和控制器组成。在过去的40年里,汽车一直使用一种称为CAN(控制器局域网络)的网络架构,它包括一个硬件标准和一个通信协议。
On the hardware side, all of the controllers piggyback on the same wire that runs through the vehicle, called the CAN bus. And just to emphasize, every item on the network has to be connected to the same main wire that runs the length of the vehicle. For this video, it's not important to understand why that is. It's just a result of the way the CAN bus system was designed in the early 1980s. Besides the controllers being wired to the CAN bus, as I said a moment ago, they're also, of course, wired into all the endpoints they manage, which are sometimes on the opposite side of the vehicle. The result is a rat's nest of connections throughout the vehicle that uses several kilometers of wire.
在硬件方面,所有控制器都连接在贯穿整个车辆的一根线上,这根线被称为CAN总线。需要强调的是,网络上的每个设备都必须连接到这根贯穿车辆全长的主线上。对于这个视频来说,理解为什么会这样并不重要,这只是CAN总线系统在20世纪80年代初设计时的结果。除了控制器连接到CAN总线外,正如我刚才提到的,它们当然也连接到了它们管理的所有终端设备,有时这些设备位于车辆的另一侧。结果就是,整个车辆内部布满了几公里长的线路,形成了一团乱麻般的连接。
With that understanding in place, let's move on to the history of Tesla's vehicle wiring, with the Model S, and then look at how that wiring system eventually evolved into the Etherloop architecture. For the Model S, released in 2012, Tesla used mostly off-the-shelf controllers, around 80%, and the remaining 20% were designed in-house. The total wire length in the vehicle was about 3 kilometers, and its total weight was about 36 kilograms. For the Model S, Tesla was just trying to get their first mass-market electric vehicle on the road, so it used a relatively conventional wiring system.
在了解这些之后,让我们继续介绍特斯拉车辆布线的历史,从Model S开始,然后看看这种布线系统如何最终演变成Etherloop架构。2012年推出的Model S,特斯拉使用了约80%的现成控制器,剩下的20%是内部设计的。整车的总线长度大约是3公里,重量约为36公斤。对于Model S,特斯拉只是试图推出他们的首款面向大众市场的电动汽车,所以它使用了相对传统的布线系统。
However, by 2017, when Tesla released the Model 3, 56% of the controllers were designed in-house. They achieved that by merging the controllers, so that one controller could look after more than one system or set of endpoints. A hypothetical example would be to use the same controller for both the front headlights and the windshield wipers. That would eliminate one of the controllers for either the headlights or the wipers, and would also mean one less set of wires to connect to the CAN bus. With dozens of controllers spread throughout the vehicle, that offered a target-rich environment. And compared to the Model S, Tesla was able to reduce the wire length in the Model 3, from 3 kilometers to 1.8 kilometers, which reduced the weight by 17 kilograms to 19 kilograms.
然而,到2017年,当特斯拉发布Model 3时,有56%的控制器是内部设计的。他们通过合并控制器实现了这个目标,使一个控制器可以管理多个系统或设备。例如,假设同一个控制器可以同时控制前灯和挡风玻璃雨刷,这样就可以减少一个前灯或雨刷的控制器,也意味着少了一组需要连接到CAN总线的电线。在整辆车中分布有几十个控制器,这为优化设计提供了丰富的目标环境。与Model S相比,特斯拉在Model 3中将电线长度从3公里减少到了1.8公里,这使得整体重量减少了17到19公斤。
The next major improvement to the wiring system for Tesla is in the Cybertruck. We don't know exactly how long the wiring harness on the Cybertruck is and what it weighs, but Pete Bannon of Tesla said that they were able to reduce the total weight of the wiring by half as compared to the Model 3. That is, despite the Cybertruck being a much larger vehicle than the Model 3, the wiring in it probably weighs less than 10 kilograms and is less than a kilometer long. That's even more impressive considering the number of endpoints in the Cybertruck increased from 273 to 368, and more endpoints means more wires. As for what those endpoints are, I imagine a number of them are for new features like the rear wheel steering and steer by wire system. Regardless, how are they able to reduce the weight of the wiring package by half for a vehicle that's much larger and has 35% more endpoints?
特斯拉线缆系统的下一个重大改进是在Cybertruck(赛博卡车)上。我们还不知道Cybertruck的线束长度和重量,但特斯拉的Pete Bannon表示,他们将线缆的总重量减少了一半,与Model 3相比。也就是说,尽管Cybertruck比Model 3大得多,其线缆的重量可能不到10公斤,长度不到一公里。考虑到Cybertruck的端点数量从273增加到368(更多的端点意味着更多的线缆),这更加令人惊叹。至于这些端点是什么,我猜其中一些用于新的功能,比如后轮转向和线控转向系统。无论如何,他们是如何在一辆更大且有35%更多端点的车辆上,将线缆的重量减少到一半的呢?
Three ways. First, they continued to merge controllers in the vehicle, just like they did from the Model S to the Model 3. Second, they switched to a 48 volt wiring system for the Cybertruck. As Tesla said at Investor Day, 48 volt wiring allows for four times less current than a typical 12 volt wiring system, which means much thinner wires that use about 75% less copper. Yes, as we've seen with the carasoft teardown of the Cybertruck, the vehicle isn't using 48 volts everywhere, but where 48 volts was used, as Monroze teardown showed, it significantly reduced the weight of the wiring. Third, for the Cybertruck, Tesla started using what Monro refers to as an ethernet ring, and Tesla refers to as Etherloop, which replaces the CAN bus used in the Model 3. By using that Etherloop, not only were they able to reduce wire weight, they were also able to reduce the number of cross-car connections from 490 in the Model 3 to 155 in the Cybertruck. As you'll recall from the beginning of the video, Tesla said the Etherloop would eliminate cross-car wiring.
有三种方式。首先,他们继续在车辆中合并控制器,就像从Model S到Model 3一样。其次,他们为Cybertruck换用了48伏的布线系统。正如特斯拉在投资者日上所说,48伏的布线系统相比于典型的12伏系统,电流减少了四倍,这意味着可以用更细的电线,铜的使用量减少了大约75%。的确,如我们在Cybertruck的拆解中看到的那样,该车并不是所有地方都使用了48伏,但正如Monroze的拆解所显示的那样,在使用48伏的地方,布线的重量显著减少。第三,对于Cybertruck,特斯拉开始使用Monro称之为以太环网(ethernet ring),特斯拉称之为Etherloop的技术,这取代了Model 3中使用的CAN总线。通过使用Etherloop,他们不仅能够减少线缆的重量,还能将跨车连接点从Model 3的490个减少到Cybertruck的155个。正如你在视频开头所记得的,特斯拉说Etherloop将消除跨车布线。
So although the Etherloop and the Cybertruck reduced cross-car wiring by 68%, it didn't completely eliminate it. Why is that? In short, it would have been nearly impossible to jump from a 12 volt CAN bus electrical system to a 48 volt Etherloop system in one step. So the Cybertruck was a necessary intermediary step between the wiring architecture in earlier vehicles and the wiring architecture that'll be used in the next-gen vehicle, which must use a full Etherloop network that's at least mostly 48 volts for their unboxed manufacturing process to work. But we're getting ahead of ourselves. Let's back up for a moment. Why would it be nearly impossible to jump from 12 volt CAN bus to 48 volt Etherloop in one step? Let's start with the controllers.
因此,虽然Etherloop和Cybertruck使车内横向布线减少了68%,但并没有完全消除它。为什么呢?简而言之,从一个12伏的CAN总线电气系统直接跳跃到48伏的Etherloop系统几乎是不可能的。所以,Cybertruck作为一个必要的中间步骤,连接了早期车辆的布线架构和下一代车辆将使用的布线架构。下一代车辆必须使用一个主要是48伏的完整Etherloop网络,以便其无框架制造过程能正常工作。但我们有点超前了。让我们回过头来。为什么从12伏CAN总线直接跳到48伏Etherloop几乎是不可能的?我们先从控制器开始讲起。
Most auto manufacturers have, for the most part, outsourced the hardware and software for their controllers. That's as opposed to Tesla, which, in effect, created a startup within the company to design in-house controller hardware and build the supply chain for it, as well as write the software. So, over time, as they gathered engineering resources and built their supply chain, the controllers startup within Tesla swallowed more of the controller designed for each new vehicle. The Cybertruck is the penultimate version, and it not only increased the in-house controller content to 85 percent, it also adopted a predominantly 48 volt architecture, the first mass produced vehicle by any manufacturer to do so. That meant the controllers had to be a native 48 volt design as well, which meant a full redesign of most of the controllers that went into the Cybertruck.
大多数汽车制造商大部分都将其控制器的硬件和软件外包出去。这与特斯拉形成了对比,特斯拉实际上在公司内部创建了一个初创团队,专门设计内部控制器硬件并建立其供应链,同时还编写相关软件。随着时间的推移,特斯拉内部的这个控制器初创团队逐步积累了工程资源并完善了供应链,每出一款新车,这个团队就负责更多的控制器设计。Cybertruck(赛博卡车)是这种方法的一个巅峰之作,它不仅将内部设计的控制器比重提高到85%,还采用了主流的48伏架构,成为首款采用这种架构量产的车辆。这意味着控制器必须是原生48伏设计,从而需要对大多数使用在Cybertruck上的控制器进行全面重新设计。
Why? Because 48 volts enable smaller controllers that use smaller wires, traces, effuses, and thermal management, such as heat sinks. That is, the Cybertruck is the biggest leap in wiring architecture that Tesla has deployed so far. But that's not all. The vehicle also uses Etherloop, which is an entirely new wiring architecture and communication protocol that replaces the Canbus network. So what exactly is Etherloop and how does it differ from Canbus? Bear in mind that much of what I'm about to cover here is speculation. As usual, it's speculation that emerged after I spent some time researching the topic. If you're an expert in vehicle networks, let me know what you think in the comments below.
为什么?因为48伏特电压使得可以使用更小的控制器、更细的电线和走线、熔断器以及热管理系统,比如散热片。也就是说,Cybertruck在电气布线架构方面是特斯拉迄今为止最大的突破。但这还不是全部。该车辆还使用了Etherloop,这是一个全新的电气布线架构和通信协议,取代了Canbus网络。那么,什么是Etherloop,它与Canbus有何不同呢?请注意,我即将讨论的很多内容都是推测。这些推测源于我在研究这一话题时的发现。如果你是车辆网络方面的专家,请在下方评论区告诉我你的看法。
Kicking things off, as I said earlier, with each new vehicle, Tesla merged more of the controllers. The implication of that is that the controllers went from being system-specific to increasingly general purpose. That means the controller hardware was increasingly defined by its software. This is what's known as software-defined hardware. As I pointed out earlier, one immediate benefit of more generalized controllers that looked after more endpoints was that it reduced the amount of wiring to the Canbus. However, for more distributed systems like brakes, cross-car wiring was still needed so that the controller could still send and receive communications to each brake. These are of course the cross-car wires that Tesla talked about eliminating on Investor Day. How could the cross-car wires be completely eliminated? In my view, by jumping in with both feet on generalized software-defined controllers and ditching the Canbus network standard. Let's take a closer look.
正如我之前所说的,特斯拉在每推出一款新车型时,都会合并更多的控制器。其影响是,控制器从原本的系统专用逐渐变为通用。这意味着,控制器的硬件越来越多地由其软件定义。这就是所谓的软件定义硬件。
正如我之前指出的一样,更通用的控制器管理更多端点的一个直接好处是,它减少了连接到Canbus总线的线缆数量。然而,对于像刹车这样的分布式系统而言,仍然需要横跨车辆的线缆,以便控制器可以发送和接收每个刹车系统的通信信号。这些线缆当然就是特斯拉在投资者日上提到的要消除的横跨车辆的线缆。
那么,怎样才能完全消除这些横跨车辆的线缆呢?在我看来,可以通过全力投入通用的软件定义控制器,并放弃Canbus网络标准来实现。让我们来仔细看看。
What if, rather than running dozens of meters of wire from a specialized brake controller to brakes on each of the four corners of the vehicle, there was a general purpose controller at each corner. That would mean the wire from the controller to the brake could be less than a meter long. That controller would also be responsible for all the other endpoints near the wheel, for things like tire pressure, suspension, and traction control, and maybe even the lights and cameras. But if each brake had its own controller, how would braking be coordinated for the vehicle as a whole? The general purpose controllers would be wired to each other with Ethernet, or network cable, to form the network. But in that network, whether it's on the controllers or central vehicle computer, there would be firmware and software of varying complexity serving each system in the vehicle, such as the braking system. That would allow the brakes to be controlled as a group with any other endpoints involved in braking, such as the brake pedal or the vehicle's central computer.
如果不是将几十米长的线从一个专用的制动控制器连接到车辆四个角的制动器,而是在每个角上放一个通用控制器,那会怎样?这样的话,从控制器到制动器的线可以不到一米长。这个控制器还可以负责车轮附近的其他终端设备,比如胎压、悬挂和牵引力控制,甚至可能包括灯光和摄像头。但是,如果每个制动器都有自己的控制器,如何协调整辆车的制动呢?这些通用控制器会通过以太网或者网络线连接起来,形成一个网络。在这个网络中,无论是在控制器上还是在车辆的中央计算机上,都会有各种复杂程度不同的固件和软件服务于车辆的各个系统,比如制动系统。这将允许制动器与任何与制动相关的其他终端设备(例如刹车踏板或车载中央计算机)一起作为一个整体来控制。
Beyond the braking system, this would of course mean that every endpoint in the vehicle would be available on the network. Whether that's video from the cameras, accelerometers in the suspension, or temperature sensors in the battery pack, they would all be able to communicate with each other to provide vehicle level surfaces, such as self-driving, ride control, and thermal management. In a sense, everything that was once running on dedicated hardware would be virtualized on the network and running on general purpose hardware. That hardware and software technology stack is what I think Tesla is referring to as the Etherloop. Let's look at CANBUS versus Etherloop as diagrams to provide another conceptual angle. Feel free to jump to the next time stamp if you feel you already grasped the Etherloop concept.
除了制动系统之外,这当然意味着车辆中的每一个端点都会在网络上可用。无论是摄像头的视频,悬挂系统中的加速度计,还是电池组中的温度传感器,它们都能够相互通信,以提供车辆级别的服务,如自动驾驶、行驶控制和热管理。从某种意义上说,所有曾经在专用硬件上运行的功能都将虚拟化在网络上,并运行在通用硬件上。我认为特斯拉称之为Etherloop的就是这种硬件和软件技术栈。让我们通过图表比较一下CANBUS和Etherloop,以提供另一种概念角度。如果你觉得已经理解了Etherloop的概念,可以直接跳到下一个时间戳。
The first thing to note for the image on screen is that for CANBUS and Etherloop, there would be both power and data wires running between the controllers and endpoints. However, the way that's designed will vary by the system. That means the lines we see here represent where there could be data and or power wires, and I'm not being specific as to which will be needed. That's because the important part is the broader system architecture. The second note is that when Tesla implements the Etherloop network in the unboxed process, it might make sense to use controllers for each sub-assembly. That's as opposed to just the four controllers I've shown here for simplicity. With that in mind, starting with the CANBUS network, each controller is responsible for a specific system, like brakes, suspension, or lights.
屏幕上的图像首先需要注意的是,对于CANBUS和Etherloop系统,控制器和终端之间会有电源线和数据线。不过,每个系统的设计方式会有所不同。这意味着我们这里看到的线条代表可能存在数据线或电源线,并且我没有具体指出哪些是需要的,因为关键是更广泛的系统架构。
第二点需要注意的是,当特斯拉在无盒工艺中实现Etherloop网络时,可能需要为每个子装配部分使用控制器,而不是像我这里为简化起见所展示的四个控制器。考虑到这一点,从CANBUS网络开始,每个控制器负责一个特定的系统,例如刹车、悬挂或灯光。
To control the brakes, for example, there needs to be a direct wiring connection from the controller to each set of brakes, which can result in cross-car wiring. Any communication that needs to occur to and from the brakes, to, for example, the brake pedal, computer, other systems, or gauges can be passed back and forth along the CANBUS. With an Etherloop network, each general purpose controller is assigned a specific zone in the vehicle and would control all of the endpoints in its local area, also known as a zonal architecture. If one of those endpoints was part of a broader vehicle system, again, like brakes, the controller would communicate through the Etherloop with all the endpoints responsible for braking. The way that communication would occur is through a series of point-to-point connections between the controllers on the ethernet cables, which form a network in the vehicle.
例如,要控制刹车,需要从控制器到每组刹车直接进行线路连接,这会导致车内布线复杂。任何需要与刹车系统进行的通信,例如刹车踏板、计算机、其他系统或仪表之间的通信,都可以通过CANBUS(控制器局域网总线)来传递。而在Etherloop网络中,每个通用控制器都被分配到车辆的特定区域,并控制该区域内的所有节点,这种方式被称为区域架构。如果其中一个节点属于更广泛的车辆系统,比如刹车系统,控制器将通过Etherloop与负责刹车的所有节点进行通信。通信的方式是通过以太网电缆上控制器之间的一系列点对点连接,在车辆内部形成一个网络。
That network would share all the data in the vehicle for all the endpoints, making every endpoint a shared resource. The end result and key takeaway here is that compared to a CANBUS network, the Etherloop network would use much less wire. That's because the controllers would be placed closer to the endpoints, and because the CANBUS would be replaced with a series of point-to-point ethernet connections, rather than using a separate wire for the data from each controller to a main CANBUS wire. So with all this potential to reduce wiring, why did no one implement an Etherloop before? First, as I said earlier, auto manufacturers have outsourced the design, manufacturing, and software of the electrical systems in their vehicles to third-party suppliers. And to make matters worse, one component will often contain parts or software from more than one supplier. So in order to make even a minor change to one part of the electrical system, it takes months to get all the parties together to start the redesign process.
那个网络将分享车辆中所有端点的数据,使每个端点成为共享资源。与CANBUS网络相比,Etherloop网络的最终结果和关键要点在于它将使用更少的电线。这是因为控制器将被放置在更靠近端点的地方,而且CANBUS将被一系列点对点的以太网连接取代,而不是每个控制器的数据都需要一根单独的线连接到主CANBUS线。因此,尽管有这么多减少布线的潜力,为什么以前没有人实现Etherloop呢?首先,正如我之前所说,汽车制造商已经将他们车辆电气系统的设计、制造和软件外包给第三方供应商。更糟糕的是,一个组件通常会包含多个供应商的零部件或软件。因此,即使对电气系统的一个小部件做出些微的改变,也需要几个月的时间才能让所有相关方聚在一起开始重新设计的过程。
Now multiply that by up to 70 controllers throughout the vehicle, and not just one change to one controller, but re-architecting all the controllers in the wiring system from the ground up. The second reason no one did Etherloop before is because on the software end, moving to an Etherloop network isn't as simple as just using the typical communication protocols used in a home network or on the internet. Let's take a closer look. The reason CANBUS has been so successful is that it's highly reliable for critical functions like brakes and has low latency. That's because with a CANBUS network, messages are prioritized in a way that, if two messages are sent at the same time, the message with the higher prioritization arrives first at its destination and is executed.
现在,把这个情况应用到整个车辆的多达70个控制器上,不仅是对一个控制器的单一改动,而是从头开始重新设计整个电路系统中的所有控制器。这也是为什么之前没有人使用Etherloop的第二个原因,因为在软件方面,转向Etherloop网络并不像使用家用网络或互联网中的典型通信协议那样简单。让我们仔细看看。CANBUS之所以如此成功,是因为它在执行刹车等关键功能时高度可靠,并且延迟低。这是因为在CANBUS网络中,消息被优先级排序,如果两个消息同时发送,优先级更高的消息会先到达目的地并执行。
That's as opposed to a typical ethernet protocol, where if two messages are sent at the same time, they collide and cancel each other out. When that happens, each of the sender's weights a random amount of time, and then resends the message. That creates greater latency. Latency is the time it takes for a network to transmit a message. Long latency times aren't acceptable in vehicles, because a fraction of a second delay could mean life or death. To solve the latency problem, like they do with most things software-related, Tesla's likely developed their own in-house ethernet communication protocol that gives priority to critical systems or messages. With all those difficulties in mind, it should explain why, said earlier in the video, that it would have been nearly impossible to jump directly from a 12-volt CANBUS system to a 48-volt Etherloop system, and why the Cybertruck was a necessary intermediary step between earlier vehicles and the next generation vehicle.
这与典型的以太网协议不同。当两条消息同时发送时,它们会发生碰撞并互相抵消。当这种情况发生时,每个发送者会等待一个随机的时间,然后重新发送消息。这会导致更高的延迟。延迟是指网络传输消息所需的时间。在车辆中,长延迟时间是无法接受的,因为一秒的延迟可能意味着生死攸关。为了解决延迟问题,像处理大多数与软件相关的事情一样,特斯拉可能开发了自己的内部以太网通信协议,优先处理关键系统或消息。结合所有这些困难,可以解释为什么在视频早些时候提到的,几乎不可能直接从12伏CANBUS系统跳跃到48伏Etherloop系统,以及为什么Cybertruck是早期车辆和下一代车辆之间必不可少的中间步骤。
It was just too much to do in one step, and we can see evidence of that in the low voltage system, where some of the wiring is still 12 volts rather than 48 volts, and in the cross-car wiring, which should have been completely eliminated if Tesla had fully moved to generalized controllers on Etherloop. It should also explain why Etherloop is just as critical, if not more critical than moving to 48 volts. For the next generation vehicle, if they continue to use 12 volts for some things, that's fine because it would have little effect on how the vehicle is manufactured. However, moving to a full Etherloop system for the unboxed process for the next generation vehicle will be a necessity. That's because the vehicle won't move down the production line as a single cage or box. It'll be built from several pieces that are merged at the end of the line. That means the vehicle can't use a typical CAN bus wiring system that has to be installed in one piece and touches every part of the vehicle.
要一步完成确实有点太多了,我们可以在低电压系统中看到这一点的证据,其中一些线路仍然是12伏而不是48伏,同样在跨车身布线中也是如此。如果特斯拉完全转移到基于Etherloop的通用控制器,这些布线应该已经完全被取消了。这也解释了为什么Etherloop和改用48伏一样甚至更为重要。对于下一代车辆,如果他们继续在某些地方使用12伏电系统,这没什么问题,因为这对车辆的制造影响不大。然而,对于下一代车辆的模块化生产过程,全面使用Etherloop系统将是必需的。因为车辆不会像传统那样作为一个单一的框架或箱体在生产线上移动,而是由多个部件在生产线末端合并而成。这意味着车辆不能使用典型的一体化CAN总线布线系统,因为这种系统需要安装在一个整体结构中并且覆盖车辆的每个部分。
It'll have to use a point-to-point Etherloop network where you can connect any controller to any other controller to gain access to the network, which in turn will allow the vehicle to snap together like Legos. Lastly, it's worth covering a few other benefits of Etherloop. First, the typical data rate for a CAN bus system is 1 to 10 megabits per second. That's as opposed to Tesla's Etherloop system, which is capable of at least 1 gigabit per second, which is 100 to 1000 times higher. That means Tesla can pipe more than just basic functions like the brakes through the Etherloop. They can put high data rate services through it like audio and video. Put another way, if you had the right connector, you might be able to plug a monitor into any of the controllers on the vehicle, access the entertainment system, and watch movies. Tesla isn't likely to allow that, but it gives you an idea of what's possible. In the Cybertruck, they're already piping the audio system through the Etherloop. In the past, the audio system would have had its own separate wiring system that piggybacked onto the CAN bus system.
它将不得不使用点对点的Etherloop网络,你可以将任何控制器连接到另一个控制器,从而接入网络,这反过来又可以让车辆像乐高积木一样组合在一起。最后,让我们看看Etherloop的几个其他优点。首先,传统的CAN总线系统的数据传输速率通常为1到10兆比特每秒。而特斯拉的Etherloop系统则能达到至少1千兆比特每秒,这是前者的100到1000倍。这意味着特斯拉不仅可以通过Etherloop输送像刹车这样的基本功能,还可以传输高数据速率的服务,比如音频和视频。换句话说,如果你有合适的连接器,就可以把显示器插入车辆的任何一个控制器,访问娱乐系统并观看电影。虽然特斯拉可能不会允许这么做,但这给你一个了解可能性的机会。在Cybertruck中,他们已经通过Etherloop输送音频系统。在过去,音频系统需要有自己单独的布线系统,并且附加在CAN总线系统上。
Now, the audio system is fully integrated into the broader vehicle network where it has access to shared power and data. A second benefit of Etherloop is that as the controllers become increasingly general purpose, Tesla may get to a point where they only have a few standardized controller designs or even a universal controller design for their vehicles. That would simplify their supply chain, vehicle design, and production, and create economies of scale that would drive down vehicle production costs. In summary, at Investor Day, Tesla said that for the electrical system in the Cybertruck, they would be moving the controllers closer to the endpoints and using ethernet to connect the controllers, which would in turn reduce cross-car wiring. I was excited about that possibility at the time and what it meant for Tesla's upcoming vehicles, but I didn't realize what a fundamental improvement it was until I started looking into it.
现在,音响系统完全集成到了更广泛的车辆网络中,它可以访问共享的电力和数据。Etherloop 的另一个好处是,随着控制器变得越来越通用,特斯拉可能会达到这样的程度:他们的车辆只需要少数几种标准化的控制器设计,甚至可能只需要一种通用的控制器设计。这将简化他们的供应链、车辆设计和生产过程,并产生规模经济效应,从而降低车辆生产成本。总的来说,在投资者日活动上,特斯拉表示,在 Cybertruck 的电气系统中,他们将把控制器移近到设备终端,并使用以太网连接控制器,这将减少车内跨车辆的布线。当时我对这种可能性感到很兴奋,因为它对特斯拉即将推出的车辆意味着什么,但我直到深入研究后才意识到这是一项多么重大的改进。
If my speculation is correct, Tesla is completely redesigning the electrical architecture of the vehicle and bringing it into the 21st century. The controllers will become a high-throughput network of communication hubs that allow access to any endpoint on the vehicle by any other endpoint and make the vehicle maximally software defined rather than limited by its hardware. That may allow Tesla to finally achieve less than 100 meters of wire in the next generation vehicle, which is something they were aspiring to do with the Model Y over four years ago, once again making the impossible merely late. Tesla's accomplished a lot in the past to dramatically simplify vehicle manufacturing, with innovations like gigacastings and the structural battery pack. But in my view, the Etherloop may end up being one of the most impressive and could take the longest for any other auto company to duplicate.
如果我的推测正确,特斯拉正在彻底重新设计车辆的电气架构,并将其带入21世纪。控制器将变成一个高吞吐量的通信网络枢纽,允许车辆上的任何端点与其他任何端点进行通信,从而使车辆更依赖于软件而不是硬件。这可能使特斯拉最终在下一代车辆中实现少于100米的电线,这也是他们在四年多前的Model Y中曾经努力达到的目标,再次将“不可能”变成“迟来的可能”。 过去,特斯拉通过像一体铸造和结构电池组等创新,显著简化了车辆制造流程。但在我看来,“以太环”(Etherloop)可能是最令人印象深刻的创新之一,而且可能需要更长时间才能被其他汽车公司复制。
That's because it's something that Tesla's been working on for about 15 years, component by component, since they designed the Model S. Other automakers that haven't developed in-house controller design expertise are probably seven to ten years behind Tesla. Some CEOs like Jim Farley appear to have recognized this and are making big moves to insource their electronics, so I'm eager to see how fast they can implement Etherloop. Lastly and importantly, Etherloop is the final and possibly the most daunting piece of making the unboxed process work for the next generation vehicle. Without it, the vehicle can't be manufactured as separate subassemblies, because using a prior art canbus wiring harness would require everything to be on the same canbus wire. With Etherloop, those subassemblies can snap together and come to life as an integrated network. More on that in the upcoming unboxed video. If you enjoyed this video, please consider supporting the channel by using the links in the description. Also consider following me on X. I often use X as a test bed for sharing ideas, and X subscribers like my Patreon supporters generally get access to my videos a week early. On that note, a special thanks to Asriel the Cat, my YouTube members, X subscribers, and all the other patrons listed in the credits. I appreciate all of your support, and thanks for tuning in.
这主要是因为自从特斯拉设计Model S以来,他们已经在逐一改进这一技术,已经有大约15年的时间了。而其他没有开发自有控制器设计专业技术的汽车制造商,可能比特斯拉落后七到十年。一些CEO,例如Jim Farley,似乎已经认识到了这一点,并且正在大动作地内部开发他们的电子设备。因此,我非常期待看到他们如何快速实施Etherloop。最后也是最重要的,Etherloop是使下一代汽车的无盒制造过程工作中的最后、也是最具挑战性的一环。没有它,汽车就无法作为独立的子组件进行制造,因为使用传统的canbus线束会要求所有东西在同一条canbus线上。而有了Etherloop,这些子组件可以组合在一起,并作为一个集成网络运作。更多内容将在即将发布的无盒视频中介绍。如果你喜欢这个视频,请考虑通过描述中的链接来支持这个频道。另外还可以考虑在X平台上关注我。我经常使用X作为分享想法的试验场地,X的订阅者和我的Patreon支持者通常能提前一周看到我的视频。特别感谢Asriel the Cat,我的YouTube会员,X订阅者和所有在片尾致谢名单中的赞助者。我非常感谢你们所有的支持,谢谢收看。