Why Thixomolded Magnesium is better than Gigacast Aluminum
发布时间 2024-01-17 14:54:15 来源
摘要
In this video I'll walk you through why Thixomolded Magnesium is better than Gigacast Aluminum. In short, it's lighter, creates ...
GPT-4正在为你翻译摘要中......
中英文字稿 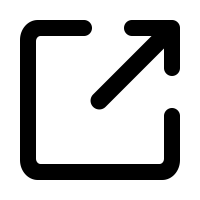
Welcome back everyone, I'm Jordan Geesege, and this is The Limiting Factor.
大家好,欢迎回来!我是乔丹·吉斯基,欢迎收看《限制因素》节目。
In the last video of the Magnesium series, I walked you through what Idra's Thixomolding process is and how it works compared to other casting processes, like aluminum gigacasting.
在镁系列的最后一个视频里,我向你展示了Idra的热塑成型工艺是什么,以及与其他铸造工艺(如铝巨型铸造)相比它是如何工作的。
With that understanding in place, today we're going to look at why Thixomolded Magnesium is in many ways better than gigacast aluminum for use in electric vehicles.
有了这个理解,今天我们将探讨为什么在电动车中,Thixomolded镁在许多方面都比gigacast铝更好。
I'll cover the cost of Thixomolded Magnesium relative to other casting methods, the hidden design benefits of Thixomolded Magnesium, whether it could be used for underbody castings, why wheels may be an even better use case, and how much magnesium we should expect in vehicles and by when.
我将介绍Thixomolded镁与其他铸造方法相比的成本,Thixomolded镁的隐藏设计优势,以及它是否可用于车身下部的铸造,为什么车轮可能是更好的应用案例,以及我们应该期待在何时以及在汽车中使用多少镁。
Before we begin, a special thanks to my Patreon supporters, YouTube members and Twitter subscribers, as well as RebellionAir.com. They specialize in helping investors manage concentrated positions. RebellionAir can help with covered calls, risk management, and creating a money master plan from your financial first principles.
在我们开始之前,特别感谢我的Patreon支持者,YouTube会员和Twitter订阅者,以及RebellionAir.com。他们专门帮助投资者管理集中仓位。RebellionAir可以帮助您进行认购认沽期权交易、风险管理,并从您的财务基本原则中制定一个金钱主计划。
Let's start with the cost of Thixomolded Magnesium, because all automakers, including Tesla, are doing everything they can to reduce the cost of electric vehicles.
让我们从镁热模成型的成本开始讨论,因为包括特斯拉在内的所有汽车制造商都在竭尽全力降低电动汽车的成本。
意思:我们首先来谈谈镁热模成型镁合金的成本,因为所有的汽车制造商,包括特斯拉,都在努力降低电动汽车的成本。
This image from Salzberger Aluminum Group, or SAG, compares the performance of a number of metalworking technologies.
这张来自Salzberger铝合金集团(SAG)的图片比较了几种金属加工技术的性能。
Let's pair back the bubble plot to the technologies that are relevant to this video. Vacuum Assisted Diecasting, Semi-Solid Diecasting, and Forging.
让我们将气泡图配对到与此视频相关的技术上。真空辅助压铸、半固态压铸和锻造。
SAG didn't provide any assumptions or notes on the slide, but I'll add some for context.
SAG在幻灯片中没有提供任何假设或注释,但我会添加一些以便理解背景。
The first assumption is that vacuum assisted die casting is just high pressure die casting with vacuum assist, which is what Tesla uses for their aluminum gigacastings. So I'll replace the words vacuum assisted die casting with aluminum gigacasting to make the image more clear.
第一个假设是真空辅助压铸仅仅是高压压铸加上真空辅助的技术,这也是特斯拉在其铝制巨型铸件中使用的方法。因此,为了让描述更清楚,我会用铝制巨型铸件来代替真空辅助压铸。
The second assumption is that semi-solid casting refers to rheocasting because this image came from a video on rheocasting. Rheocasting was covered in the last video, and the short story is that, like Thixomolding, casting uses a semi-molten slurry to produce high quality castings at a similar cost to Thixomolding. So I'll replace the words semi-solid casting with Thixomolding because the cost and quality are the same, but Thixomolding is what this video is about.
第二个假设是半固态铸造指的是流变铸造,因为这张图片来自一个关于流变铸造的视频。上一个视频中讲到了流变铸造,简而言之,像热挤压成型一样,铸造使用半熔膏糊来生产具有高质量的铸件,成本与热挤压成型相似。因此,我会将半固态铸造这个词替换成热挤压成型,因为成本和质量是相同的,但是这个视频所讲的是热挤压成型。
The third assumption is that all three of these metalworking technologies are using aluminum, because the SAG video I pulled this image from was strictly focused on aluminum.
第三个假设是,这三种金属加工技术都是使用铝材,因为我从SAG视频中提取出这张照片的视频专注于铝材。
With those assumptions in place, the question is, where do the cost and quality of Thixomolded magnesium sit relative to the quality and cost of Thixomolded aluminum?
在这些假设的基础上,问题是,相对于Thixomolded铝的质量和成本,Thixomolded镁的成本和质量如何?
As for quality, we can keep the quality of Thixomolding in the same position, because whether magnesium or aluminum is used in the Thixomolding process, the part quality will remain the same. Why? Because by quality, I mean porosity. Or porosity means higher quality, which in turn means stronger and more ductile parts, because the parts contain fewer voids and more solid metal. That is, quality isn't a measure of strength and ductility, but the ability of a process to maximize those properties regardless of which metal is used.
就质量而言,我们可以保持Thixomolding的质量在同一个位置上,因为无论在Thixomolding过程中使用镁还是铝,零件质量都将保持不变。为什么呢?因为在质量方面,我指的是孔隙率。或者说孔隙率意味着更高的质量,进而意味着更强和更具延展性的零件,因为零件中的空隙较少,固态金属较多。也就是说,质量不是强度和延展性的评估标准,而是一种无论使用哪种金属都能最大化这些性质的能力。
As for cost, the image shows that Thixomolded aluminum is slightly more expensive than gigacast aluminum and significantly less expensive than forging. But what happens when we swap out the Thixomolded aluminum for Thixomolded magnesium?
就成本而言,图像显示Thixomolded铝比gigacast铝略贵,但远比锻造成本低很多。那么,当我们将Thixomolded铝替换为Thixomolded镁时会发生什么呢?
First, magnesium has a lower melting temperature than aluminum, a lower heat of fusion and its lower density, so it requires less energy to both heat the metal for casting and to cool the part to solidify it. That means lower production costs and potentially faster cycle times.
首先,镁的熔点比铝低,熔解热也较低,而且密度较小,因此在铸造时需要较少的能量来加热金属并使零件冷却固化。这意味着更低的生产成本和可能更快的循环时间。
Second, magnesium is less reactive with the steel dye than aluminum. But lower reactivity means that magnesium eats up less of the steel dye with each casting that aluminum does. For example, at the same temperature, the dyes for magnesium last about 80% longer. Those dyes cost hundreds of thousands of dollars each, so the fact that the dyes last longer with magnesium adds to the cost advantage of magnesium Thixomolding over aluminum Thixomolding.
其次,与铝相比,镁对钢模具的反应性较低。但是,较低的反应性意味着每次浇铸时镁对钢模具的侵蚀较小。例如,在相同的温度下,镁的模具使用寿命比铝长大约80%。这些模具每个都价值数十万美元,因此,镁在Thixomolding相比铝具有更低的模具使用成本,这是镁材料的成本优势之一。
Third, in North American and European markets, magnesium costs significantly more per ton than aluminum. However, the strength-to-weight ratio of magnesium is significantly higher than aluminum. That means when factoring in the strength-to-weight ratio against cost per ton, magnesium is currently only slightly more expensive. As a side note, if you'd like to know why advanced high-strength steel isn't used for everything despite its low cost, watch my gigacasting economics video.
第三点,在北美和欧洲市场上,镁每吨的成本要显著高于铝。然而,镁的强度与重量的比率也显著高于铝。这意味着在将强度与重量比率和每吨成本相比时,镁目前只略微更昂贵。值得一提的是,如果您想知道为什么尽管成本低廉,先进的高强度钢并没有被用于所有领域,请观看我的巨型铸造经济学视频。
Let's be conservative and say that the current additional cost of magnesium feedstock balances out the savings from its lower energy costs for heating and cooling and lower dye replacement costs. If that's the case, the cost of Thixomolded Magnesium should be roughly on par with the cost of Thixomolded aluminum. So for the moment, I'll keep the bubble for Thixomolding in the same position and rename it Magnesium Thixomolding.
我们保守一点来说,目前镁合金原材料的额外成本可以抵消其较低的加热和冷却能源成本以及较低的染料更换成本。如果是这样的情况,脱模镁合金的成本应该与脱模铝合金的成本大致相当。因此,暂时我会将这个气泡保持在原处,并将其命名为镁脱模成型。
The fourth point on cost is that we have to take into account effective cost. What do I mean by effective cost? For each kilogram of weight you remove from an EV, you can reduce the size of the other components required to move that vehicle around, such as the battery, brakes, motors, suspension, and structural reinforcement. In the first video of the series, I did some very rough back-of-the-napkin math and concluded that for every 2.2 kilograms of weight removed from the vehicle, one 4680 sized battery cell and the packaging around that battery cell could be removed from the vehicle. I also assumed that currently the battery cell and packaging material would cost about $10. Given that I don't expect Tesla to start using Thixomolding for a couple of years, and battery prices will come down over that time period, let's assume $8 saved for each 2.2 kilograms of weight reduction.
成本的第四点是我们必须考虑到有效成本。我所说的有效成本是什么意思呢?当你从电动汽车中减去每公斤的重量时,你可以减小其他组件的尺寸,如电池、刹车、电机、悬挂和结构加固,以保证车辆的运动。在这个系列的第一个视频中,我进行了一些简单的计算,得出的结论是,每减去2.2公斤的重量,就可以减去一个4680型号大小的电池单体和该电池单体周围的包装。我还假设目前电池单体和包装材料的成本约为10美元。考虑到我不指望特斯拉在未来几年内开始使用Thixomolding,而电池价格在这段时间内将会下降,我们可以假设每减去2.2公斤的重量可以节省8美元。
The front and rear Giga castings in the average Tesla weigh about 80 and 65 kilograms, respectively, or 145 kilograms in total. If magnesium castings are 33% lighter, that means a savings of 48 kilograms. That would save 22 battery cells or $176 in just the battery pack. There would also be cost savings in the motor, inverter, brakes, suspension, and vehicle structure, which could easily push the savings to $200 to $300 per vehicle. The bubble plot just shows the part level cost, so the implication is that if we take into account the cost savings of lighter weight parts and EVs, the effective cost of the parts at the vehicle level could be at cost parity or even lower than Giga cast aluminum parts.
特斯拉平均前后Giga铸件重约80和65公斤,总重为145公斤。如果镁铸件重量减轻33%,那意味着节省48公斤。这将节省22个电池单元,或者电池组仅需省下176美元。在电机、逆变器、制动系统、悬挂和车身结构方面也能节省成本,这使得每辆车的节省金额可能轻松达到200至300美元。气泡图仅显示零部件水平的成本,因此含义是,如果我们考虑到轻量化零部件和电动汽车的成本节约,零部件在整车水平的实际成本可能与Giga铸铝部件持平甚至更低。
For the fifth point on cost, earlier I used the words current additional cost of magnesium feedstock. That is, currently magnesium is expensive and costs more than aluminum, but that'll likely change as the decade progresses. As I pointed out in the first video of the series, part of the reason why magnesium is expensive is because it's produced at lower volumes than its nearest competitor, aluminum, and we're still using processes to produce magnesium that are about 80 years old. But with the technology improvements and scaling that are expected for magnesium this decade, prices should drop. This image from S&P Global shows that magnesium should reach cost parity with aluminum by 2030.
对于成本这一点,我之前使用了“当前镁原料的额外成本”这个词组。也就是说,目前镁的价格比铝高,但是随着年代的推移,这种情况可能会改变。正如我在这个系列的第一个视频中指出的那样,镁价格昂贵的部分原因是因为其产量较其最近的竞争对手铝要低,而且我们目前仍在使用大约80年历史的镁生产工艺。但是随着预期在本十年内针对镁的技术改进和扩大规模,价格应该会下降。S&P Global的这张图显示,到2030年,镁的成本应该会与铝持平。
If that happens, when factoring in the strength-to-weight ratio against cost per ton, magnesium parts will cost about a third less than aluminum parts. That means even if we don't factor in the effective cost of magnesium parts at the vehicle level, even at the part level they should be cheaper than Giga cast aluminum parts by 2030. Furthermore, cost modeling done by Magrathia indicates that they expect to produce magnesium that not only reaches cost parity with aluminum, but that's actually cheaper than aluminum by 2030. I'll talk more about Magrathia in the next video and how they intend to hit that cost target.
如果发生了这种情况,考虑到强度与重量之比与每吨成本,镁制零件的成本将比铝制零件便宜大约三分之一。这意味着即使我们在车辆级别不考虑镁制零件的有效成本,即使在零件级别上,到2030年它们也应该比Giga型铝合金零件更便宜。此外,Magrathia进行的成本建模表明,他们预计到2030年将生产出不仅达到与铝合金成本持平的镁材料,而且实际上比铝合金更便宜。我将在下一个视频中详细讨论Magrathia以及他们打算如何实现这个成本目标。
What all this means is that I expect even with conservative assumptions, thick-so-molded magnesium castings should be at cost parity at the part level with thick-so-molded aluminum, slightly cheaper than aluminum Giga casting when factoring in vehicle level savings and potentially significantly cheaper than aluminum Giga casting by 2030. If we factor in improvements in extraction technology and increased magnesium supply, with cost out of the way, let's move on to the design benefits of thick-so-molded magnesium.
所有这一切的意思是,即使采取保守的假设,通过厚度一致的模铸镁合金件应该在部件层面上和厚度一致的模铸铝合金件的成本相当,在考虑车辆层面的节省时略低于铝合金千克级铸件,而到2030年时,可能会比铝合金千克级铸件便宜得多。如果我们考虑到提取技术的改进和镁供应增加,成本问题解决后,让我们转向模铸镁的设计优点。
As I said earlier, thick-so-molding uses semi-moulton metal instead of fully molten metal. That fundamentally changes the way the metal behaves in the dye through three dynamics. First, fully molten metal expands and contracts more than semi-moulton metal during the casting process. That means the castings shrink as they cool, which makes them stick to the dye and means the parts can warp as they shrink and need to be scrapped.
正如我先前所说,厚毛坯采用半熔融金属而非完全熔融金属。这从根本上改变了金属在染料中的行为方式,具体表现为三个方面。首先,完全熔融金属在铸造过程中的膨胀和收缩比半熔融金属更大。这意味着铸件在冷却过程中会收缩,从而导致它们粘附在染料上,同时也意味着零件在收缩过程中可能会变形,需要废弃。
Second, fully molten metal is more reactive and chemically attacks the dye more aggressively than semi-moulton metal, which means the castings done with molten metal stick to the dye more strongly when they're removed. This is in addition to the fact that aluminum is more fundamentally reactive with the dye, which I mentioned earlier.
其次,全熔融金属比半熔融金属更具反应性,并更加侵蚀染料,这意味着使用全熔融金属铸造的产品,在取出时更容易与染料黏附在一起。这还要加上铝与染料之间的基本反应性更高,就像我之前提到的那样。
Third, as I showed in the last video, fully molten metal experiences turbulent flow when it's injected into the dye. That turbulence traps air, creates porosity, and reduces the quality of the castings. That's as opposed to semi-moulton metal, which creates a non-turbulent laminar flow when it's injected into the dye that results in less porosity.
第三点,就如我在上个视频中所展示的,完全熔化的金属在注入模具时会经历湍流流动。这种湍流会困住空气,产生多孔性,并降低铸件的质量。与之相反,半熔融的金属在注入模具时会产生非湍流层流流动,从而减少多孔性。
Those three dynamics mean that fully molten metal is more difficult to cast than semi-moulton metal. And that means that parts cast with an aluminum gigacasting process have more design restrictions than parts made with a magnesium-thixome-molding process.
这三个因素意味着完全熔化的金属比半熔化金属更难铸造。这意味着通过铝巨型铸造工艺制造的零件比镁热塑造造型工艺制造的零件有更多的设计限制。
With regards to the first two dynamics, the fact that the parts are more likely to shrink and stick to the dye and react with and stick to the dye mean that every part that's designed for an aluminum gigacasting process has to be shaped in a way that allows it to pop out of the dye more easily. That's done with a slope on the walls of the parts called the draft angle. That means if there's an ideal that an engineer wants to design a part to, the draft angle forces the design of the part away from that ideal, which might mean a part that's not as strong or weighs more. For gigacast aluminum, the minimum draft angle is 2 to 3 degrees, whereas for thixome-molded magnesium, it's 0 to 1.5 degrees.
关于前两种动力学,事实上零件更容易收缩并黏附在染料上,并与染料发生反应并黏附在一起,这意味着每个设计用于铝基巨型铸造工艺的零件必须呈现出易于从染料中弹出的形状。这是通过零件墙壁上的斜度,也称为脱模锥角来实现的。这意味着如果一个工程师想要设计一个符合理想要求的零件,脱模锥角会迫使零件的设计偏离这个理想,可能意味着零件不够强壮或重量更重。对于巨型铝铸件,最小脱模锥角为2至3度,而对于热挤压成型的镁合金而言,最小脱模锥角为0至1.5度。
Next, a combination of the first and third dynamics, shrinkage and turbulent flow that leads to porosity, mean that for gigacast aluminum, a portion of the dye is set aside to channel the turbulent flow in a way that reduces defects, and to provide a reserve of molten metal to draw from to help compensate for shrinkage. This is called gating. What this means is that for each unit of metal that's used in a thixome molding process, more of it goes to the final part rather than being wasted as gating material that has to be stripped off, scrapped, and recycled. So if both an aluminum gigacasting machine and a thixome-molded magnesium machine have a maximum shot weight of 20 kilograms, the actual final part weight of the thixome molding machine will be closer to 20 kilograms than for the gigacasting machine.
接下来,第一和第三动态的组合,即收缩和湍流流动导致多孔性。对于超大铝铸件来说,染料的部分被保留下来以引导湍流流动,从而减少缺陷,并提供一定的熔融金属储备以补偿收缩。这被称为流道设计。这意味着在这个压铸工艺中,每单位金属中更多的材料被用于最终零件的制造,而不是浪费作为流道材料必须拆去、报废和回收。因此,如果铝超大压铸机和热挤压镁合金机的最大喷射重量都是20公斤,热挤压机制造出的最终零件的实际重量将更接近20公斤,而不是超大压铸机。
Finally, as for the third dynamic, lower turbulence and porosity, by itself it has two knock-on effects. First, it means the minimum wall thickness for magnesium thixome molding is 0.8 millimeters versus 2 millimeters for gigacast aluminum. If that design benefit carries through to larger gigascale thixome-molded parts, it may allow engineers to thin out parts of the casting that weren't able to be made thinner with a gigacasting process, meaning lighter parts. The second benefit of lower porosity is higher part consistency. The location and concentration of where porosity forms in cast parts is random. That means some parts are stronger or more ductile than others. So when a part is designed, it has to be designed so that the weaker or less ductile parts are still up to spec, which to a certain extent means the part has to be overbuilt. With higher part consistency, the parts don't need to be as overbuilt, which means lighter parts.
最后,对于第三个动态要素,较低的湍流和多孔度本身会产生两个连锁效应。首先,这意味着镁渗流成型的最小壁厚为0.8毫米,而超大铝铸造的最小壁厚为2毫米。如果这种设计优势也适用于更大规模的渗流成型零部件,那么工程师可以将铸件中无法通过超大铸造工艺变得更薄的部分变薄,从而实现零部件的轻量化。较低的多孔度的第二个好处是更高的零部件一致性。铸造零部件中多孔度形成的位置和浓度是随机的。这意味着某些部件比其他部件更强壮或更具韧性。因此,在设计零部件时,必须确保较弱或不太韧性的部分仍符合规范,这在一定程度上意味着零部件必须过度设计。有了更高的零部件一致性,零部件就不需要过度设计,从而实现零部件的轻量化。
The net effect of a smaller draft angle, thinner minimum wall thickness, more efficient use of material, and greater part consistency means that with thixome molding, engineers can make a bigger part that's more effective for a specific use case for the same kilogram of metal. And that's independent of any of the properties of the metal itself. It's strictly a design benefit inherent to thixome molding casting technology.
借助翻译中的易读性,我给出一种表达方式:
使用较小的起模斜角、较薄的最小壁厚、更高效的材料利用以及更大的零件一致性,综合效果表明,在同等重量的金属下,使用糊状金属注射成型技术(thixome molding),工程师可以制造出更适合特定用途的更大的零件。而这与金属本身的任何特性无关,严格来说,这是糊状金属注射成型技术固有的设计优势。
Now that we understand the cost and design aspects of thixome-molded magnesium, where could it be used? Onscreen is a list of parts that auto manufacturers are already using magnesium for or are exploring using magnesium for. Let's focus on what I consider to be the most interesting use cases.
既然我们已经了解了热挤压成型镁合金的成本和设计方面,那么它可以在哪些领域应用呢?屏幕上显示了汽车制造商已经在使用镁合金的零部件或者正在探索使用镁合金的零部件。让我们重点关注我认为最有趣的应用案例。
Underbody castings and wheels. Chinese researchers are already experimenting with what appears to be underbody castings. I say appears to be because the part is blurred out. However, it is confirmed to be a car body in the article, and the shape and size for me indicates that it's an underbody casting that would weigh at least 40 to 50 kilograms. That's because a similar-sized aluminum, rear underbody casting in the model Y weighs about 65 kilograms, and a magnesium casting would weigh about a third less. The question is, what type of casting technology did the Chinese researchers use? The 20-kilogram shot weight that Edra is teasing is the largest that I know of for semi-solid casting like thixome molding. So my guess is that they used standard high-pressure die casting, or vacuum die casting rather than thixome molding. Regardless, overall, I think they have the right idea about where casting technology is headed for vehicles.
车身底板和车轮。中国研究人员似乎已经在尝试底板铸件。我说似乎是因为这部分已被模糊处理。然而,该文章确认它是一辆汽车的车身,根据它的形状和大小,我认为它是一个重量至少为40到50公斤的底板铸件。这是因为机型Y中类似尺寸的铝合金后底板铸件约重65公斤,而镁铸件则会轻约三分之一。问题是,中国研究人员使用了哪种铸造技术?Edra展示的20公斤的注射重量,在凝固态铸造(如浆态造型)中是我所知的最大值。所以我猜他们使用的是标准的高压压铸,或者是真空压铸,而不是浆态造型。无论如何,总的来说,我认为他们对于车辆铸造技术的发展方向有正确的认识。
Larger magnesium castings. Edra's first gigascale thixome molding machine is expected to have a shot weight of 20 kilograms, and although that's not quite large enough for an underbody casting, it's likely just the beginning. As I said in the last video, just as the size of gigacasting machines nearly tripled in the last few years, the same is likely to happen with thixome molding machines. And in my view, the shot weight for magnesium thixome molding may not even need to triple from 20 kilograms to make castings that are the size of a 60 to 80 kilogram aluminum casting. And that's for three reasons. First, magnesium is less dense than aluminum, so it can produce parts that are 50% larger for the same shot weight. Second, as I said earlier, thixome molding makes more efficient use of the casting metal because it requires less gating. So a greater portion of the metal is used for the actual part than to accommodate for turbulence and shrinkage. Third, Tesla recently revealed that they're designing their newer castings in a way that encourages the flow of molten metal through the die. For the casting on screen, they used a 6,500 ton gigapress, which just a couple of years ago would have required an 8,000 ton gigapress. With all that mine, I wouldn't be surprised if by 2026 or 2027, Idra has a second or third generation gigascale thixome molding machine that can produce front and rear underbodies that are equivalent in size to the front and rear gigacastings used in the Model Y. In the meantime, it's a target rich environment for Idra's thixome molding machines that have a 20 kilogram shot weight.
更大的镁铸件。Edra的第一台超大型锻模机预计会有20公斤的注射重量,虽然这还不足以用于底部铸件,但这只是一个开始。正如我在上一个视频中所说的,在过去的几年里,大型铸造机器的尺寸几乎增长了两倍,热压成型机也可能会发生同样的情况。在我看来,镁铝热压成型的注射重量甚至不需要从20公斤增加到60到80公斤的铝铸件的尺寸。这有三个原因。首先,镁比铝密度小,所以使用相同的注射重量可以生产比铝件大50%的零件。其次,正如我之前所说,热压成型对铸造金属的利用更高效,因为它需要较少的冲孔。因此,更大一部分的金属用于实际零件,而不是用于补偿紊流和收缩。第三,特斯拉最近透露他们正在设计他们的新铸件,以鼓励熔融金属通过模具流动。在屏幕上的铸件中,他们使用了一台6500吨的超大型压力机,而仅仅几年前,这需要一台8000吨的超大型压力机。考虑到所有这些,如果到2026或2027年时Idra推出第二或第三代的超大型热压成型机,能够生产与Model Y中使用的前后超大型铸件相同尺寸的前后车身,我不会感到惊讶。与此同时,对于Idra的注射重量为20公斤的热压成型机来说,这是一个有潜力的发展环境。
On that note, why does Idra refer to the 20 kilogram shot weight for magnesium thixome molding as gigascale? If current, underbodies gigascale castings weigh at least 65 kilograms. I can't speak for Idra, but for me, it's because the 20 kilogram casting is produced on the same Idra gigapress machines as the 65 kilogram castings. The only difference is that the 20 kilogram casting requires Idra's thixome molding piston injection unit that's bolted onto the gigapress, which I covered in the last video. Lastly, before we move on to magnesium wheels, an interesting side benefit of a magnesium underbodies casting is that magnesium is great at turning vibrational energy into heat that's quickly dissipated, also known as damping. If you're curious about the science behind damping, the information on screen does a good job of explaining it. We don't need to get into that much depth today. The key takeaway is that magnesium has several times more damping capacity than aluminum. That means if it's used for structural and suspension parts, it can create a vehicle with better ride quality while maintaining a firm body structure.
在这一点上,为什么Idra将镁合金熔模注塑的20公斤射重称为巨型尺度?如果当前的车身零部件的巨型铸件重量至少为65公斤。我不能代表Idra说话,但对我来说,这是因为20公斤的铸件是在与65公斤铸件相同的Idra巨型压力机上生产的。唯一的区别是20公斤的铸件需要Idra的熔模注塑活塞注射装置,它被螺栓固定在巨型压力机上,我在上一个视频中介绍过。最后,在我们转向镁合金车轮之前,一种镁合金车身铸件的有趣附带好处是,镁合金在将振动能量转化为迅速消散的热量方面表现出色,也被称为阻尼。如果你对阻尼背后的科学原理感兴趣,屏幕上的信息能很好地解释。我们今天不需要过多深入讨论这个。关键要点是镁合金的阻尼能力比铝多几倍。这意味着如果用于结构和悬挂部件,它可以创造出具有更好悬挂品质的车辆,同时保持坚固的车身结构。
Let's move on to wheels. The use of cast magnesium wheels was fairly widespread in the 1950s and 1960s because they're about 25% lighter than aluminum wheels and about 40% lighter than steel wheels. However, among other things, they were prone to corrosion, so for the most part, they were abandoned by the auto industry. The one exception was high performance race cars and other performance vehicles because corrosion resistance wasn't a key requirement. Then in the 1990s, racers started using forged magnesium wheels because they're even lighter than cast magnesium wheels. That's because, as I showed earlier, forged parts offer the highest part quality and therefore the highest strength and ductility. But the drawback of forging is that it's the most expensive metalworking technology.
让我们继续谈论车轮。在20世纪50年代和60年代,铸造镁合金轮毂的使用非常普遍,因为它们比铝合金轮毂轻约25%,比钢制轮毂轻约40%。然而,它们容易受到腐蚀等问题的困扰,因此在大部分情况下,汽车行业已经放弃了使用这种轮毂。唯一的例外是高性能赛车和其他性能车辆,因为防腐性不是关键要求。然后在20世纪90年代,赛车手开始使用锻造镁合金轮毂,因为它们比铸造镁合金轮毂更轻。这是因为,如前面所示,锻造零件提供了最高的零件质量,因此具有最高的强度和延展性。但是锻造的缺点是它是最昂贵的金属加工技术。
You probably see where I'm going with this. Thixo molded magnesium produces parts that are nearly as high quality as forged parts but at a much lower cost. So I'm expecting to see the resurrection of cast magnesium wheels except this time using Thixo molding.
你可能已经看出我的意思了。Thixo模塑镁生产的零件几乎与锻造件一样具有高质量,但成本要低得多。因此,我预计会看到镁合金轮毂的复兴,但这次会使用Thixo模塑技术。
What about the corrosion concerns that caused magnesium wheels to be abandoned? A lot has changed in 50 years. As I showed in the first video of the series, with newer alloys, corrosion is now a solved problem. And if more corrosion resistance is needed, the wheels can be coated, which is often done with aluminum parts as well.
那么,关于导致镁合金车轮被弃用的腐蚀问题怎么样了呢?在过去的50年里,发生了很多变化。正如我在系列第一个视频中所展示的那样,借助更先进的合金材料,腐蚀问题现在已经得到解决。而且,如果需要更多的耐腐蚀性能,车轮可以进行涂层处理,这在铝制零件上也经常采用。
As a result, magnesium wheels on the market today can have up to a 10 year warranty and can even outlast aluminum wheels. Some people might also raise flammability as a concern, but it's the same deal. Even a dash of calcium can dramatically reduce flammability. If you'd like to know more about that, watch the first video of the series.
因此,目前市场上的镁合金轮毂可以提供长达10年的保修期,并且甚至比铝合金轮毂寿命更长。一些人可能会担心其可燃性问题,但实际上并不是什么大问题。即便添加一点钙,也可以显著减少可燃性。如果你想了解更多相关信息,请观看本系列的第一个视频。
All that aside and getting to the main point, why are lighter wheels such a big deal? They have a big impact on vehicle efficiency because they have lower rotational inertia. In simple terms, what that means is that the lighter the wheel, the easier it is for the motors to spin that wheel, meaning greater vehicle efficiency and range and faster acceleration.
撇开这一切,来谈谈主要观点,为什么轻质车轮如此重要?它们对车辆效率有很大影响,因为它们具有较低的旋转惯量。简单来说,这意味着车轮越轻,电机旋转车轮的阻力就越小,这意味着更高的车辆效率和续航里程以及更快的加速。
For example, the aluminum 20 inch uber turbine wheels used on performance Tesla Model 3s and Y's weigh 13 kilograms each. Cast magnesium wheels of the same size weigh about 10.2 kilograms and forged magnesium wheels 7.4 kilograms. Fix-o-molded magnesium wheels would probably weigh about 8 to 8.5 kilograms.
例如,用于性能特斯拉Model 3和Y的20英寸铝合金超级涡轮车轮每个重量为13公斤。相同尺寸的铸造镁合金车轮约重10.2公斤,锻造镁合金车轮重为7.4公斤。预计Fix-o-molded镁合金车轮重约为8至8.5公斤。
That means a weight savings of about 5 kilograms per wheel, or 11 pounds, by using fix-o-molded magnesium wheels instead of cast aluminum wheels. For a total weight savings of 20 kilograms or 44 pounds for all four wheels.
这意味着使用固定-模塑镁合金车轮而不是铸铝轮,每个车轮的重量可以减少约5公斤或11磅。对于四个车轮来说,总共的重量减轻了20公斤或44磅。
That's roughly in line with the test that Tesla owners Silicon Valley did, where they reduced the total tire and wheel weight by 52 pounds or 23.6 kilograms. The result was that they saw a 4-6 percent range improvement. So with a 20 kilogram weight savings, the result would probably be closer to 3-5 percent.
这大致符合特斯拉所有者在硅谷进行的测试结果,他们减少轮胎和车轮的总重量达到了52磅或23.6千克。结果是他们看到了4-6%的续航里程改善。因此,如果减少20千克的重量,结果可能会更接近3-5%的续航里程改善。
That 3-5 percent range improvement would likely be more than the range improvement provided by replacing the aluminum underbody castings with magnesium, which would improve vehicle range by around 1-2 percent. That is, the wheels would provide double or triple the range improvement while using roughly 1-3 the magnesium.
将铝合金底板铸件更换为镁合金可能只会提高车辆续航里程约1-2%,而3-5%的提升范围更可能是由车轮所提供的。换句话说,车轮在使用大约1-3倍的镁合金的同时,提供了双倍或三倍的续航里程提升。
Furthermore, with fix-o-molded magnesium wheels, the vehicle would not only see a 3-5 percent range improvement. The wheels would be cheaper than cast aluminum wheels. They would provide better ride quality through improved damping, and the car would also be more nimble and accelerate faster because the lighter weight wheels are more responsive. Much the same way that wearing tennis shoes makes you more agile than wearing heavy boots.
此外,使用固定模具的镁合金车轮不仅可提高3-5%的续航里程,而且这种车轮比铸造铝车轮更便宜。它们通过改善阻尼提供更好的行驶质量,而且由于更轻的重量,车子也更加敏捷,加速更快。就像穿上网球鞋比穿重靴子更能增加灵活性一样。
Before we move on, it's worth making two more points on magnesium wheels. First, the technology to cast even one fix-o-molded magnesium wheel, which would weigh at least 8 kilograms, only arrived last year when 10 kilogram shot weight fix-o-molding machines hit the market. Now that the technology is there to cast wheels that large and even larger, in the next 3-5 years, fix-o-molded magnesium wheels could become a trend.
在我们继续之前,值得再提两点关于镁合金车轮。首先,制造一个重量至少为8公斤的固定型镁合金车轮的技术直到去年才出现,当时10公斤射融合机器上市。现在,已经有了制造如此大尺寸甚至更大的车轮的技术,在未来的3-5年内,固定型镁合金车轮可能会成为一种趋势。
Second, bear in mind that the 3-5 percent improvement is for a large wheel used on a performance vehicle. For smaller efficiency vehicles, they tend to use smaller rims and narrower tires to improve range and reduce production costs. So it might not make sense to use magnesium wheels on, for example, a robo-taxi. But I can't see a good reason why higher end vehicles like the Model 3, Y, S, X, or even the Cybertruck wouldn't use fix-o-molded magnesium wheels.
其次,请记住,3-5%的改进是针对性能车辆上使用的大尺寸车轮而言的。对于较小效率车辆来说,他们倾向于使用较小的车圈和较窄的轮胎以提高续航里程并减少生产成本。因此,在例如机器人出租车这样的车辆上使用镁合金车轮可能没有意义。但我看不出为什么高端车型,如Model 3、Y、S、X或甚至Cybertruck不会使用固定成型镁合金车轮,没有一个好理由。
Now that we've covered the benefits of fix-o-molded magnesium and its uses, how much magnesium can we actually expect to be used in vehicles? McKinsey expects that at least 5% of the weight of a new vehicle produced in 2030 will be magnesium, which on average is about 100 kilograms of magnesium per vehicle, or enough to replace the underbody castings.
现在我们已经讨论了固定成型镁合金及其用途的好处,那么在汽车中实际可以预期使用多少镁合金呢?麦肯锡(McKinsey)预计,到2030年,每辆新生产的汽车中至少将有5%的重量是镁合金,平均约为每辆车100公斤镁合金,足够替代底盘铸件。
On the high end, they estimate it would be up to 16% of the vehicle, which in my estimation would mean replacing all of the parts we see on screen with magnesium. Maybe more. Either way, analysts are expecting large increases in the amount of magnesium used in vehicles, because currently the average vehicle is less than 1% magnesium. That 1% tends to be used in smaller parts like the screen mount for Tesla's vehicles. But that'll change with the ability to do larger ultra-high quality fix-o-molded magnesium castings.
在高端汽车领域,他们估计镁的使用比例可能高达汽车总重的16%,依我看来,这意味着我们需要将屏幕上所见的所有零部件都更换成镁制品,甚至可能更多。不管怎样,分析师预计在汽车中使用镁的数量将大幅增加,因为目前平均汽车中的镁含量不到1%。这1%往往用于像特斯拉汽车的屏幕支架这样的较小零部件上。但随着能够进行更大尺寸、超高质量的模铸镁铝件制造,这种情况将会改变。
The question is, why are analysts so bullish on magnesium and what factors are they looking at?
问题是,为什么分析师对镁如此看好,他们看重哪些因素?
This spider chart for 2020 from S&P Global's automotive materials team in Detroit shows the performance of magnesium and aluminum across a range of properties. Magnesium is in black and aluminum is in blue. For most of the properties, aluminum outperforms magnesium. So at a glance, from a historical perspective, the typical criticisms of magnesium's cost and performance are valid. Of course, this information is now 4 years old. What does the future look like?
这是来自S&P全球汽车材料团队在底特律制作的2020年蜘蛛图,展示了镁和铝在各个性能指标上的表现。镁以黑色表示,铝以蓝色表示。在大多数性能指标上,铝的表现优于镁。所以从历史角度来看,对于镁的成本和性能的典型批评是合理的。当然,这些信息已经过去了4年。未来的情况会如何呢?
By 2030, thanks to factors like fix-o-molding and expanded magnesium production, the performance of magnesium in the spider chart improves dramatically, and magnesium becomes much more competitive with aluminum. But this is S&P's base case. What about a more bullish estimate? In the image on screen, Magrithia took S&P's 2030 estimate and overlaid it with their own projections with a pink dotted line. Let's take a closer look at the key properties, what they mean, and how they compare between magnesium and aluminum, and what the implications are.
到2030年,得益于固定模塑和扩大镁生产等因素,镁在蜘蛛图中的性能有了显著提升,与铝相比,镁变得更具竞争力。但这只是S&P的基本情况。那么对于更乐观的估计呢?在屏幕上的图像中,Magrithia将S&P的2030年估计与他们自己的预测进行了叠加,用粉色虚线表示。让我们更仔细地看一看关键特性,它们的意义以及镁和铝之间的比较,以及这些有什么影响。
First, as I said earlier, Magrithia's goal is to produce magnesium cheaper than aluminum, whereas S&P Global expects magnesium to reach cost parity with aluminum. Either way, both forecasts are bullish for magnesium, and cost is the single most important property on the spider chart. Why? Despite the drawbacks of magnesium due to its light weight, at the right price it's considered a useful replacement for aluminum. Depending on what the magnesium to aluminum price ratio is, sometimes overall, it's actually preferable to use magnesium.
首先,正如我之前所说,Magrithia的目标是比铝更便宜地生产镁,而标普全球预计镁将与铝达到成本平衡。无论哪种方式,这两个预测对镁都是看涨的,成本是蜘蛛图上最重要的属性。为什么呢?尽管镁由于其轻质而存在一些缺点,但以合适的价格,它被认为是铝的有用替代品。根据镁与铝的价格比率,有时候实际上更倾向于使用镁。
So if the price of magnesium can be reduced on a sustained basis, and its performance increases, it will become the dominant light weight structural metal. The next most important property is availability. If there's not a relatively broad supply chain for magnesium with a number of suppliers, manufacturers won't build their products around it. Even in S&P's base case scenario, availability improves dramatically between 2020 and 2030. Magrithia, on the other hand, has aggressive scaling plans that I'll cover in the next video.
如果镁的价格能够持续降低,并且其性能增加,那么它将成为主导轻便结构金属。下一个最重要的性质是可供性。如果没有一个相对广阔的镁供应链和多个供应商,制造商就不会围绕它来构建产品。即使在标准普尔的基本情况下,可供性在2020年和2030年之间大幅改善。另一方面,Magrithia有积极的扩大计划,我将在下一个视频中详细介绍。
Next, energy absorption is likely referring to buckling. Buckling refers to how the geometry of a structure responds to compression and bunches up like an accordion. For example, if you look closely at Tesla's gigacastings, you can see wavy accordion-like geometry designed to do exactly that. Buckle. Stipness is a function of how much stress a part can take before it deforms, or for those familiar with stress strain curves, it's the slope of the line.
接下来,能量吸收很可能指的是弯曲。弯曲指的是结构的几何形状对压缩作用的响应,并像手风琴一样扭曲起来。例如,如果你仔细观察特斯拉的巨型铸件,你会看到像手风琴一样波浪形的几何形状,旨在实现这一目的。扭曲。刚度是零件在变形之前能承受的应力量的函数,或者对于那些熟悉应变曲线的人来说,它是曲线的斜率。
As for toughness, they're likely referring to fracture toughness, which is how resistant a material is to crack propagation. In 2030, energy absorption, stiffness, and toughness are close enough to aluminum that magnesium will likely be able to serve as an alternative in most use cases. And notably, magnesium in 2030 outperforms the numbers for aluminum from 2020 in both toughness and stiffness, 3 versus 2 and 4 versus 3, respectively, and it barely falls short in terms of energy absorption.
就强度而言,他们可能指的是断裂韧性,即材料抵抗裂纹扩展的能力。到2030年,能量吸收、刚度和韧性与铝非常接近,镁很可能成为大多数用例中的替代品。值得注意的是,镁在2030年的韧性和刚度方面表现优于2020年的铝材,分别为3比2和4比3,从能量吸收方面略有不及。
At 9 versus 10, that is, S&P assumes that by 2030, magnesium will have considerably better stiffness and toughness compared to the aluminum of 2020, while achieving 90% of its energy absorption. That should put to bed the frequent arguments I've heard against magnesium suitability for automotive use cases because it can't compete with aluminum in terms of its structural properties. That may have been true in the past, but new alloys and better processes are being developed each year.
在2030年的时候,标普(S&P)预测镁合金在刚性和韧性方面将明显优于2020年的铝合金,同时可以实现90%的能量吸收。这将为那些声称镁合金在汽车应用中的适用性不如铝合金的争论画上句号。以往这可能是正确的观点,但是每年都在开发新的合金和更好的工艺。
Furthermore, it's the whole spider chart that matters not just one or two properties. The fact that magnesium will offer lighter weight parts at equal to or lower cost than aluminum means that it'll offer better value for money for EVs. Where cost and weight considerations dominate. The other material properties could be accommodated for with fractionally thicker parts, while still maintaining the cost and weight advantages.
此外,整个蜘蛛图(指材料性能的多个指标)才是重要的,不仅仅是其中一两个特性。镁材料能够以与铝材料相等甚至更低的成本提供更轻的部件,这意味着对于电动汽车而言,它将提供更好的性价比。在成本和重量方面的考虑占主导地位的情况下,其他材料特性可以通过稍厚一些的部件来满足,并同时保持成本和重量的优势。
As a side note, I've also heard criticisms of the fatigue and creep performance of magnesium. With thixomolding, magnesium performs as well as, or better than, gigacast aluminum for both properties. However, that's deeper than we need to go today, and I may do another video in the future that dives deeper into properties like creep, fatigue, stiffness, and energy absorption.
值得一提的是,我也听说过对镁材疲劳和爬行性能的批评。在凝固成形过程中,镁的性能在这两个方面与超硬铸铝相比表现得同样好,甚至更好。然而,这已经深入到我们今天不需要去研究的程度,我可能会在未来再做一个深入探讨爬行、疲劳、刚度和能量吸收等性能的视频。
In summary, in my view, a number of factors are converging that may mean that by the end of the decade, thixomolded magnesium will replace gigacast aluminum as the best way to reduce the cost and weight of vehicle components.
总之,依我之见,有多个因素正在趋于一致,这可能意味着到本十年末,熔模铸造镁将取代巨型压铸铝成为降低汽车零部件成本和重量的最佳方式。
First, EVs can afford to pay a premium for lightweight materials because a lighter weight vehicle needs, for example, smaller motors, batteries, and brakes, which are high cost components. That'll drive increased demand for magnesium because it's the lightest structural metal, allowing for a greater reduction in high cost components than aluminum.
首先,电动汽车可以负担得起轻质材料的溢价,因为较轻的车辆需要较小的电动机、电池和制动器等高成本组件。这将推动对镁的需求增加,因为它是最轻的结构金属,相比铝能够更有效地减少高成本组件的重量。
Second, in the past few decades, alloys have been developed that reduce the flammability of magnesium, increase its corrosion resistance, and improve its overall performance, which further increases its utility and therefore demand.
其次,在过去的几十年中,已经开发出了多种合金来降低镁的易燃性,提高其耐蚀性,并改善其整体性能,进一步增加了其实用性和因此需求量的增加。
Third, the factors that we covered in depth today, magnesium thixomolding will be able to produce parts that are higher quality, use the space and the die more efficiently, extend the die life, and allow for part designs that are closer to the optimum part design rather than a design that's been compromised by limits on draft angles and wall thicknesses. This will also increase the demand for magnesium.
第三,我们今天详细讨论的因素是,镁热塑造将能够生产出更高质量的零件,更有效地利用空间和模具,延长模具寿命,还能够实现更接近最佳零件设计的设计,而不是因为结构角度和壁厚的限制而产生折衷的设计。这也将增加对镁的需求。
Fourth, thanks to the increased demand due to EVs, better alloys and thixomolding, the supply of magnesium will increase, which will lower prices and increase availability. That in turn will mean thixomolded parts will become increasingly compelling versus gigacast aluminum parts.
由于电动汽车需求的增加,以及更好的合金和热塑成型技术,镁的供应将会增加,从而降低价格并增加可用性。这反过来意味着与超大铸造铝件相比,热塑成型零件将变得越来越有吸引力。
So when will we see large thixomolded parts in, for example, a Tesla? First, Idra has to get their gigascale thixomolding machines on the market, which will happen in 2025 based on their presentation. That means a year or two after that before we see those machines in an actual factory at high production rates, which means 2026 or 2027.
那么,我们何时会在特斯拉等车型中看到大型渗铸零部件呢?首先,Idra公司必须将他们的超大规模渗铸机器推向市场,他们的演示表明这将在2025年实现。这意味着在此之后一年或两年的时间,我们才能在实际工厂中看到这些机器以高产量运行,即2026年或2027年。
Second, there needs to be an increase in the availability and a decrease in the cost of magnesium, which in my view are the primary limiting factors for the shift to magnesium. I expect minor increases in production and availability by 2026 and a much larger increases by the end of the decade, which should correspond with cost decreases. That is, I don't expect thixomolded magnesium parts to really hit the mainstream for another two years.
其次,镁的供应量需要增加,成本需要降低,这是我认为对于转向镁材料的主要限制因素。我预计到2026年,生产和供应将略有增加,而到本十年末将会有更大的增长,这应该会伴随着成本的降低。也就是说,我不认为热挤压镁合金零部件真正进入主流市场还需要再过两年。
And after that, the extent to which magnesium thixomolding becomes dominant will depend on magnesium supply. The shift may start with smaller parts and then expand to larger parts as greater magnesium supply becomes available. But when magnesium supply does begin to scale in earnest, the shift to thixomolded magnesium will be as rapid and nearly as significant as Tesla's shift from stamped underbodies to gigacast aluminum underbodies.
之后,镁压铸的主导程度将取决于镁的供应情况。随着更大数量的镁供应可用,这一转变可能始于较小的零部件,然后逐渐扩展至较大的零部件。但当镁供应真正开始大规模增加时,转向镁压铸将像特斯拉从冲压底盘转向千吨铸造铝底盘一样迅速且具有重要意义。
We'll talk more about scaling in the next video when I cover magnesium from seawater.
在下一个视频中,当我介绍海水中的镁时,我们会更详细地讨论扩展问题。
As a final note, this video series is focusing mainly on the automotive use case for magnesium, but the broader use cases are endless in a world where everything is getting lighter. For example, magnesium might make a great material to make a robot skeleton out of to increase efficiency and battery life.
作为最后的说明,这个视频系列主要关注镁在汽车用途上的应用案例,但在一个一切都越来越轻的世界中,它的广泛应用领域是无限的。例如,镁可能是一个很好的材料选择,能够制作出用于增加效率和电池寿命的机器人骨架。
Needless to say, I'm excited to see what the future holds for magnesium and interested to read your comments about your thoughts and predictions below.
毫无疑问,我对镁的未来充满期待,也很想读到您对此的想法和预测的评论。
If you enjoyed this video, please consider supporting the channel by using the links in the description. Also, consider following me on X. I often use X as a test bed for sharing ideas and X subscribers like my Patreon supporters generally get access to my videos a week early.
如果你喜欢这个视频,请考虑通过描述中的链接支持本频道。同时,请考虑在X上关注我。我经常将X作为一个分享想法的试验台,而关注我的X订阅者(就像我的Patreon支持者一样)可以提前一周观看我的视频。
On that note, a special thanks to Siddharth Atreya for your generous support of the channel, my YouTube members, X subscribers, and all the other patrons listed in the credits. I appreciate all of your support and thanks for tuning in.
在此,特别感谢Siddharth Atreya对该频道的慷慨支持,以及我的YouTube会员、X位订阅者和名单上所有其他赞助人。感谢大家的支持,并且感谢大家收看。