Idra Enters the Thixomolded Magnesium Game // But What is It?
发布时间 2023-12-20 13:53:07 来源
摘要
Idra Group, which pioneered the Gigacasting machines that Tesla uses for their massive underbody castings, is now working on ...
GPT-4正在为你翻译摘要中......
中英文字稿 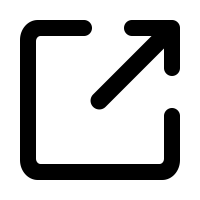
Welcome back everyone, I'm Jordan Geisigee, and this is The Limiting Factor. Eidra Group, which pioneered the gigacasting machines that Tesla uses for their massive underbody castings, is now working on gigascale machines for chip cast magnesium, also known as Thixomolded Magnesium. This matters because die cast magnesium parts weigh roughly a third less than die cast aluminum parts. The question is, what is Thixomolding? Today I'll answer that question along with how it compares to other casting technologies and the engineering challenges that Eidra and their partners had to solve to make Thixomolding work for large castings. Before we begin, a special thanks to my Patreon supporters, YouTube members and Twitter subscribers, as well as RebellionAir.com. They specialize in helping investors manage concentrated positions. RebellionAir can help with covered calls, risk management, and creating a money master plan from your financial first principles.
欢迎大家回来,我是乔丹·盖西吉,这是《极限因素》节目。Eidra Group是一家首创吉加斯铸造机的公司,特斯拉使用这种机器进行大型底盘铸造。现在他们正在研发吉加规模机器,用于芯片铸造镁,也称为热塑成形镁。这很重要,因为压铸镁件的重量大约比铝件轻三分之一。问题是,什么是热塑成型?今天我将回答这个问题,以及与其他铸造技术的比较以及Eidra及其合作伙伴为使热塑成型适用于大型铸件而必须解决的工程挑战。在我们开始之前,特别感谢我的Patreon支持者、YouTube会员和Twitter订阅者,以及RebellionAir.com。他们专门帮助投资者管理集中头寸。RebellionAir可以帮助处理盖被式认购、风险管理,并基于您的金融基本原则制定财务规划。
First, for those concerned about the flammability or corrosion characteristics of magnesium, I'd recommend watching the first video of the magnesium series linked in the card above. In short, the flammability and corrosion concerns around a magnesium aren't the primary challenge for the adoption of magnesium for vehicle structures because they're solved problems. The primary challenge is actually size limits on high quality mass produced castings and cost and availability. In this video and the next, I'm tackling the challenge of large, high quality mass produced castings in a subsequent video on Magrathia, I'll cover cost and availability as well as how magnesium can be produced with net zero emissions.
首先,对于那些担心镁的可燃性和腐蚀特性的人,我建议观看上面链接的镁系列的第一个视频。简而言之,镁的可燃性和腐蚀问题并不是镁车身结构被广泛采用的主要挑战,因为这些问题已经解决了。主要的挑战实际上是高质量大规模生产铸件的尺寸限制以及成本和可用性。在这个视频和接下来的视频中,我将解决大规模高质量铸件的挑战,而在随后的Magrathia视频中,我将讨论成本和可用性,以及镁如何实现零排放生产。
To understand what magnesium Thixomolding is, let's start with familiar territory. The gigacasting process Tesla uses for aluminum, which I'll just call gigacasting for short, and go from there. With gigacasting, the molten aluminum is held in a crucible near the casting machine, ladled into the shot sleeve, and then injected into the die at high pressure. Besides the high injection pressure, the die is also under vacuum to reduce trapped air and the cast part. That's important because trapped air leads to porosity, which can reduce the quality of the cast part. Next, the molten aluminum is rapidly cooled using large banks of thermal management units. After the metal solidifies, the casting is removed and then trimmed.
为了理解镁挤压成型是什么,让我们从熟悉的地方开始。特斯拉使用的铝材料镁挤压工艺,我简称为挤压,然后从那里开始。在挤压过程中,熔融的铝材料被放置在靠近铸造机的坩埚中,然后被舀入注射套筒中,再以高压被注入铸模中。除了高压注射外,铸模还处于真空状态,以减少受困的空气和铸件中的气孔。这很重要,因为受困的空气会导致气孔,从而降低铸件的质量。接下来,熔融的铝材料通过大型热管理装置迅速冷却。金属凝固后,铸件被取出并修整。
With Magnesium Thixomolding, the first difference is of course the metal used. When magnesium is in its molten state, there's a risk that under the right conditions, it can react with oxygen in the surrounding air and start on fire. That reactivity varies a lot depending on how hot the molten material is, whether it's pure magnesium or an alloy and the surface area to volume ratio of the magnesium. That is, it's not a major issue with good processes, but it's still a risk-percasting magnesium that aluminum doesn't have to the same extent. Thixomolding levels the playing field and effectively eliminates the reactivity and ignition risk submagnesium. How? The injection chamber is connected to a hopper that holds chip magnesium. It houses an auger and it's surrounded by an array of heating elements. The magnesium chips from the hopper are compressed and conveyed by the auger and heated by the heating elements until they become a slurry that contains both molten magnesium and solid magnesium, like shaved ice in water. That slurry is in what's called a thixotropic state, which is how Thixomolding gets its name. It's a molding process that uses a thixotropic liquid. We don't need to get into what a thixotropic liquid is today. The key point is that we're talking about a viscous or slow-flowing metal slurry that's only partially molten.
随着镁变形模塑技术的应用,第一个区别当然是所使用的金属。当镁处于熔化状态时,存在一种风险,即在适当的条件下,它会与周围空气中的氧气发生反应并引发火灾。这种反应性取决于熔融物料的温度、是纯镁还是合金以及镁的表面积与体积比。也就是说,在良好的工艺中这并不是一个主要问题,但仍存在一定的风险,而铝则没有这种程度的风险。镁变形模塑技术消除了镁的反应性和点火风险。具体如何实现呢?注射室连接有一个容纳镁碎屑的料斗。料斗中有一个螺旋输送器,并且周围有一系列的加热元件。料斗中的镁碎屑经过螺旋输送器的加压和传送,并在加热元件的加热下变成含有熔融镁和固体镁的浆状物,就像水中的冰屑一样。这种浆状物处于所谓的糊塑态,这也是镁变形模塑技术得名的原因。它是一种使用糊塑液的成型工艺。今天我们不需要深入讨论什么是糊塑液。关键是我们要谈论的是一种粘稠或慢流动的部分熔化的金属浆料。
As a side note, the viscosity of the slurry can vary quite a bit depending on the ratio of solid to molten metal. It can range from the consistency of warm butter to solid enough that it can form slugs for injection into the dye.
顺便提一下,浆料的粘度在固体与熔融金属的比例下可能有很大的变化。它的粘度范围可以从温热奶油一样的稠度,到足够坚实以至于能形成注入模具的物块。
Getting back on track, the Thixomolding process limits the reactivity of the magnesium with the oxygen in the air in four ways. First, magnesium doesn't become reactive with air until it's molten, and the hotter the molten metal, the more reactive it is. With Thixomolding, the magnesium is in a semi-moulton state, which means only a fraction of the metal is molten and reactive, and the metal that IS molten is cooler than the metal that would be used with a fully molten process.
让我们重新回到正题,Thixomolding工艺通过四种方式来限制镁与空气中的氧气反应。首先,在镁熔化之前,镁不会与空气发生反应,而且熔融的金属越热,它的反应性就越强。使用Thixomolding工艺,镁处于半熔融状态,这意味着只有部分金属熔化且具有反应性,而且熔化的金属温度比完全熔融工艺中使用的金属要低。
Second, argon gas is often used in the hopper to displace oxygen. Argon is a nerd and it's not a greenhouse gas, and it's used in a sealed chamber so it's less of a concern than cover gases, which I'll cover in a moment.
其次,氩气常用于料斗内,用来取代氧气。氩气是一种无害物质且不属于温室气体,且它被用于密封的容器内,因此相对于保护气体,它的影响较小,接下来我会详细讨论保护气体。
Third, even if argon wasn't used, the air between the magnesium chips is forced out by the compression of the auger before they even reach a temperature where they might react with oxygen.
其次,即使没有使用氩气,镁屑之间的空气也会在螺旋器的压缩作用下被迫排出,甚至在它们达到可能与氧气反应的温度之前。
Fourth, when the magnesium IS injected into the dye, just like with gigacasting, the dye contains no air because it's under vacuum. After the magnesium cools, it's then removed and trimmed for use in a vehicle. So end to end, with Thixomolding, molten magnesium is never exposed to oxygen, which eliminates flammability risks in confined spaces like factories.
第四,当镁被注入染料中时,就像用于巨型铸造一样,由于处于真空状态,染料中不含空气。镁冷却后,便会被取出并修整,以便在车辆中使用。因此,可以说整个热塑成型过程中,熔融镁永远不会暴露在氧气中,这消除了在厂房等封闭空间中的可燃风险。
On that note, Thixomolding is easily confused with rheocasting. Rheocasting is short for rheopectic casting. Rheopectic, in this case, is again just another word for the semi-moulton metal used in the casting process. Technically, a rheopectic liquid is different than a thixotropic liquid, but for the purposes of today's video, the characteristics of the two liquids is the same. They're both liquids that contain a suspension of solid particles, or slurries. What differs and what matters is the process involved in casting them.
在此基础上,Thixomolding很容易与流态铸造混淆。流态铸造是流动凝胶铸造的简称。在这种情况下,流态指的是铸造过程中使用的半熔态金属的另一个词。从技术上讲,流态液体与可塑性液体不同,但在今天的视频中,这两种液体的特性是相同的。它们都是含有固体颗粒悬浮物或浆料的液体。不同的是铸造这两种液体所涉及的过程和重要性。
With rheocasting, the process is very similar to gigacasting. The metal is heated until it's fully molten in a crucible near the casting machine, but because it's magnesium, this time a cover gas is used in the crucible. A cover gas is a heavy inert gas that sits on top of the molten metal to protect it from reacting with the surrounding air, and it also reacts with the surface of the molten metal to form a protective film.
在流变铸造中,该过程与巨浇铸非常相似。金属在靠近铸造机的坩埚中加热,直到完全熔化,但这次使用了坩埚中的保护气体,因为金属是镁。保护气体是一种重型惰性气体,它覆盖在熔化金属的顶部,以保护其免受周围空气的反应,并与熔化金属的表面反应形成一层保护膜。
At some point between being melted in the crucible and transferred to the shot sleeve, the metal is cooled to a semi-moulton steak. There are two ways that can be done. The first is to ladle the metal from the crucible to a cooling unit, where it's formed into a slug for injection into the die. The second is to cool the metal in the crucible to a semi-moulton steak, and then pump it into the injection chamber with a transfer tube.
在从坩埚中被熔化到转移到射液套筒之间的某个时刻,金属会被冷却到半熔融状态。有两种方法可以实现这一点。第一种方法是将金属从坩埚中舀出,放入冷却设备中,并成形为注射模具中的块。第二种方法是将金属在坩埚中冷却至半熔融状态,然后通过传输管将其泵入注射腔室中。
After the metal is transferred to the injection chamber, it's injected into the die, the metal is cooled to its solid state, and then it's removed for trimming. The rheocasting process creates a number of challenges and disadvantages.
在将金属转移到注射室后,将其注入模具中,金属被冷却至固态,然后移除以进行修整。温铸工艺会带来许多挑战和不利因素。
First, the most commonly used cover gases for rheocasting are SF6 and SO2, which are sulfur hexafluoride and sulfur dioxide. These gases are non-toxic, but because they can displace air and therefore oxygen, they do pose an asphyxiation risk to workers in confined spaces. That's a small risk when managed properly, but a risk nonetheless. Additionally, sulfur hexafluoride is over 23,000 times more potent as a greenhouse gas than CO2.
首先,现在流变铸造中最常用的覆盖气体是SF6和SO2,即六氟化硫和二氧化硫。这些气体虽然无毒,但因为它们可以排除空气和氧气,所以在封闭空间中给工人带来窒息风险。如果正确管理,这种风险很小,但仍然存在。此外,六氟化硫作为温室气体的强效性是二氧化碳的23000倍以上。
Because the magnesium is heated to a higher temperature, and then cooled to its semi-moulton state, rather than being heated just enough to partially melt the metal-like fixo molding, rheocasting uses more energy and wastes more of it than the thixo molding.
由于镁材料被加热到更高的温度,然后冷却至半熔融状态,而不是仅加热到部分熔化的金属状固态铸造,流变铸造比凝固态铸造使用更多的能量,也会浪费更多能量。
With the ladle method, there's a brief period of time where the molten metal is fully exposed to air. That's a fire hazard. One that can be controlled with good processes, but it still adds additional risk.
使用舀取法时,熔融金属会在短暂的时间内完全暴露在空气中。这样会引起火灾的危险,尽管可以通过良好的流程进行控制,但仍然增加了额外的风险。
Despite the challenges of rheocasting, it does offer one primary benefit. After the parts are cast and trimmed, the scrap can be directly recycled by throwing the scrap metal back in the crucible and re-melting it. That's opposed to the thixo molding process, where the trimmings have to be melted, formed into ingots, and then re-chipped before being put back in the hopper and melted again for casting.
尽管流变铸造存在挑战,但确实有一个主要优点。在零件铸造和修整之后,废料可以直接通过将废金属投入坩埚并重新熔化来进行回收利用。这与浆态模塑工艺形成对比,该工艺需要先将修整料熔化,成形成锭,然后再被再次切碎后放回料斗,再次熔化以进行铸造。
So overall, rheocasting and thixo molding are comparable processes, but thixo molding is a safer process because the molten magnesium is never exposed to air and it doesn't require a cover gas, which is generally either a potent greenhouse gas and or an additional human hazard in confined spaces.
总的来说,流变铸造和凝胶模压是可比较的工艺,但凝胶模压是一种更安全的工艺,因为熔融镁永远不暴露在空气中,而且不需要覆盖气体,通常覆盖气体要么是一种强效温室气体,要么在封闭空间中增加人类的危险。
Those are likely the primary reasons why Idra decided to pursue a thixomolding process for magnesium casting rather than rheocasting.
这些很可能是Idra决定选择镁铸造的热挤压成形工艺而不是流态成形的主要原因。
With that said, in my view, another potential reason is the simplicity.
话虽如此,在我看来,另一个潜在的原因是简易性。
With rheocasting, the molten and semi-m molten metal is handed off or transferred between different machines or different parts of the casting machine, whereas with thixo molding, everything happens within the injection chamber.
使用流动铸造法时,熔融和半熔融的金属在不同机器或铸造机的不同部位之间进行移交或转移;而在糊状成型中,所有操作都发生在注射室内。
That should allow for continuous temperature monitoring from chipped metal to the final cast part.
这将允许从金属加工到最终铸造零件的温度进行连续监测。
Why does temperature control matter? Because for semi-m molten metal, small changes in temperature can have a big impact on the liquid to solid ratio, which affects its flowability during injection.
为什么温度控制很重要?因为对于半熔融金属来说,温度的小变化可以对液固比例产生很大影响,而这又会影响注射过程中金属的流动性。
Flowability has a big impact on the ability of the semi-m molten metal to completely fill the die during injection and the porosity of the cast part.
流动性对半熔态金属在注射过程中完全填充模具以及铸件的孔隙度具有重大影响。
So temperature control is a big factor in quality control.
温度控制是质量控制中的一个重要因素。
On that note, earlier in this video and in the last video, I said that size limits on high quality mass-produced castings were one of the factors holding magnesium back as a structural metal.
在此之前,在这个视频和上一个视频中,我提到高质量大规模生产铸件的尺寸限制是制约镁作为结构金属的因素之一。
Size limits is shorthand for a number of requirements that go hand in hand to make large magnesium castings that are commercially viable for mass-produced vehicles.
尺寸限制是一系列要求的简称,它们相互关联,以制造出对于大规模生产的汽车来说具有商业性的镁合金铸件。
Let's take a closer look.
让我们仔细看一下。
By size limits, I mean parts larger than 10 kilograms.
通过“尺寸限制”,我指的是大于10千克的零件。
By quality, I primarily mean low porosity, which makes for stronger and more ductile parts.
就质量而言,我主要指的是低孔隙度,这会使零件更强硬、更耐拉伸。
And by mass-produced, I mean hundreds of thousands of parts per year.
而且当我说大规模生产时,是指每年数十万个零件。
In the past, there wasn't a casting process for magnesium that could do all of these things at once.
过去,没有一个可以同时完成所有这些工作的镁铸造工艺。
Some people might point out that Tesla's gigacasting machines produced large, high quality parts and at a high rate.
一些人可能会指出,特斯拉的巨型铸造机可以高速生产大型高质量部件。
Why not just swap out the aluminum for magnesium?
为什么不只是将铝替换为镁呢?
表达意思:为什么不考虑将铝材换成镁材?
That's a good point.
这是一个好观点。
Cold chamber high-pressure die casting machines like the Gigapress can actually be used to cast magnesium by swapping out the aluminum in the crucible with magnesium and by using a cover gas.
冷室高压压铸机(例如Gigapress)实际上可以通过将铝熔炉更换为镁,并使用覆盖气体来铸造镁。
That's an oversimplification, but it's the general idea.
这只是一个过于简单化的说法,但它传达了大致的思想。
Interestingly, the ability of gigacasting machines to cast magnesium is how Eadro was able to design their thixome molding machines as a bolt-on option for their gigacasting machines.
有趣的是,由于巨型浇铸机的能力,能够浇铸镁合金,这正是Eadro能够将他们的稠化成型机设计为巨型浇铸机上的可插拔选项的原因。
That is, a company like Tesla could buy the thixome molding unit, attach it to their existing gigacasting machines and start producing thixome molded magnesium castings.
也就是说,像特斯拉这样的公司可以购买这种熔模单位,将其连接到现有的大型铸造机上,开始生产熔模化的镁铸件。
So again, if that's the case, why not just forgo the expensive thixome molding unit and just use fully molten magnesium with a gigacasting process?
那么,如果是这种情况,为什么不放弃昂贵的压铸成型机,而是采用完全熔化的镁材料,并采用巨型铸造工艺呢?
It's because casting parts with thixome molded magnesium is superior to casting parts with molten magnesium.
这是因为使用注射模压镁铸件比使用熔融镁铸件更优。
Why? Starting with the quality requirement, with gigacast aluminum, when the aluminum is injected into the die, the pressure is so high and the molten metal is so flowable that the aluminum is essentially sprayed into the die.
为什么呢?从质量要求开始,使用铸造型铝材料时,当铝液注入模具时,由于压力非常高且熔融金属非常流动性,铝基本上是喷射入模具的。
That creates turbulence that traps air and results in porosity.
这造成了气流的湍流,困住了空气并导致了多孔性的结果。
That's as opposed to viscous semi-miltin metal that creates a laminar flow that's less susceptible to trapping air.
这是与黏稠的半固态金属相对应的,它形成较不容易困住空气的层流流动。
That means that despite the fact that gigacasting machines use a vacuum to reduce the porosity of cast parts, thixome molded parts have even lower porosity.
这意味着尽管巨形铸造机使用真空来降低铸件的孔隙率,但逆模铸造件的孔隙率甚至更低。
Why does porosity matter? Low porosity can dramatically increase the strength and ductility of cast parts.
为什么孔隙率很重要?低孔隙率可以显著提高铸件的强度和延性。
The image on screen shows that of the casting techniques included in the plot, high pressure die cast parts have the lowest quality.
屏幕上显示的图像表明,在故事情节中,高压模铸件的质量最低。
Next is vacuum assisted die casting, which I assume is the vacuum assisted high pressure die casting Tesla used for gigacasting, which has low to medium quality.
接下来是真空辅助压铸,我认为这是特斯拉用于大型压铸的真空辅助高压铸造技术,质量在中低水平。
Finally, semi-solid casting.
最后,半固态铸造技术。
在这句话中,表达的是对一种类型的铸造技术——半固态铸造技术的提及,并且强调这是最后一项技术。
My solid casting encompasses thixome molded and rheocast parts, which have such high quality that they're competitive with forged parts.
我的实心铸件包括由高品质的锻件相媲美的Thixome模压铸件和Rheocast铸件。
That's important for magnesium because it tends to be a weaker and less ductile metal than aluminum.
这对镁来说非常重要,因为它通常比铝更脆弱和不易塑性变形。
So in order to make cast magnesium competitive with cast aluminum, thixome molding is the best option.
为了使镁铸件与铝铸件具有竞争力,糊状铸造是最佳选择。
As a side note, with regards to the cost continuum shown on this slide, I'll take you deeper into that in the next video of the series.
顺便提一下,在这张幻灯片上显示的成本连续性方面,我将在系列的下一个视频中更详细地介绍。
Next, as for speed, magnesium thixome molding produces parts at a similar rate to aluminum gigacasting.
接下来,就速度而言,镁浆铸造的速度与铝巨型铸造相似,可以生产出类似的零件。
For example, on screen is a comparison between a hot chamber die casting machine on the left and a thixome molding machine on the right.
例如,屏幕上左侧是一个热室压铸机,右侧是一个铸态成型机的比较。
I timed the thixome molding machine at 44 seconds per cycle and the die casting machine at about 50 seconds.
我将压铸成型机调定为每个循环44秒,而压铸机大约为50秒。
So the thixome molding machine is a bit faster.
所以,这台粘度模压机速度稍微快一些。
Although the speed advantage that magnesium has here could, in part, be related to the size or complexity of the part being cast, I have confirmed with people in the industry that it's generally true that thixome molding is typically similar in speed to gigacasting.
尽管镁在这里具有的速度优势可能部分与所铸件的尺寸或复杂程度有关,但我已经向行业内的专业人士确认,熔模成形通常与超大型铸造的速度相近,这一点是普遍适用的。
Moving on to part size, up until a few years ago, the maximum part size for thixome molding was less than 5 kilograms.
转到零件尺寸方面,直到几年前,热态模压的最大零件尺寸不到5公斤。
And it was only in the last year that part size reached 10 kilograms.
直到去年,零件的大小才达到了10公斤。
How was Edra able to increase the part size to 20 kilograms and is 20 kilograms large enough for gigacastings?
埃德拉是如何将零件尺寸增加到20公斤的?20公斤的尺寸是否足够大呢,足以用于巨型铸件?
First, as I said a moment ago, thixome molding requires precise temperature control for high quality parts. But there's another reason why temperature control is important outside of quality. If the magnesium goes from being semi-moulton in the auger to solid, it can destroy the auger, which, including downtime, can cost millions of dollars to replace. If Edra is increasing the size limit of thixome molded castings, it means they've solved the temperature control challenge. My guess is with better electronics and control software. The second challenge for large thixome molded parts was backflow.
首先,正如我刚才所说的,微晶成型要求精确的温度控制以制造高质量的零件。但是除了质量,温度控制的重要性还有另一个原因。如果镁合金从螺旋输送机内的半熔状态变为固态,就会损坏螺旋输送机,这将导致数以百万计的美元用于更换,包括停工时间的损失。如果Edra正在增加微晶成型铸件的尺寸限制,这意味着他们已经解决了温度控制的挑战。我猜测是通过更好的电子设备和控制软件。对于大型微晶成型零件的第二个挑战是回流现象。
The auger not only conveys and compresses the magnesium chips, it acts as a piston to inject the shot into the die. So it has to be able to both rotate freely and create a tight enough seal to generate high injection pressures. Edra solved that by making the auger and the injection piston separate functions. The auger conveys the molten metal to an injection chamber.
螺杆不仅能传送和压缩镁屑,还起着将注射料推入模具中的活塞作用。因此,它必须能自由旋转,并创建足够密封以产生高注射压力。埃德拉通过将螺杆和注射活塞分开功能来解决这个问题。螺杆将熔化金属传送到注射腔。
Then, as far as I can tell from the image, the auger moves forward to seal against injection chamber pressure at the tip of the auger. And the piston generates the necessary pressure to force the metal into the die. Edra calls this thixotropic piston injection, or TPI, and it should sidestep both the backflow issue and allow for much higher injection pressures and larger cast parts.
根据图片来看,螺旋机头向前移动以在机头处抵御注射腔压力。活塞则产生所需的压力,将金属强行注入模具中。Edra称之为"流变活塞注射",也即TPI,它应该能够避免回流问题,并且允许更高的注射压力和更大的铸件尺寸。
While we're on the topic of injection pressures, it's worth noting that even though thixome molding requires higher injection pressures, it actually requires lower clamping forces for a given part size. Why? As I explained in my original gigacasting video, the die is like a giant catcher's mitt. But in this case, the baseball is a 60 kilogram slug of molten aluminum that's injected into the die at 22 miles per hour. That's why gigacasting machines require massive clamping forces of over 6,000 tons, and they weigh over 400 tons. With thixome molding, the shot of metal is the consistency of soft butter rather than a liquid, which results in slower injection speeds. Or a slower moving molten metal baseball, and therefore requires a smaller die, or catchers mitt for a given weight of material. The implication here is that gigacasting machines that companies like Tesla already use for aluminum should be large enough to cast full underbody castings made of magnesium, and that the limiting factor for casting size is Idra's ability to increase the injection pressure for the thixotropic piston injection process.
说到注射压力的话题,值得注意的是,尽管浆态模压需要更高的注射压力,但对于给定的零件尺寸,它实际上需要更低的夹紧力。为什么呢?就像我在我的原始巨型铸造视频中解释的那样,模具就像一个巨大的接球手套。但在这种情况下,棒球是一个60千克的熔化铝块,以时速22英里注入到模具中。这就是为什么巨型铸造机需要超过6000吨的大夹紧力,它们的重量超过400吨。而在浆态模压中,金属的注射物的一致性类似于软黄油,而不是液体,这导致注射速度较慢。或者说是一个移动速度较慢的熔融金属棒球,因此对于给定的材料重量,需要较小的模具,或者接球手套。这意味着像特斯拉这样的公司已经用于铝材的巨型铸造机应该足够大,可以铸造由镁制成的完整下盖铸件,并且铸造尺寸的限制因素是Idra增加浆态活塞注射工艺的注射压力的能力。
Furthermore, for the same shot weight, magnesium can make a larger casting because it's a lighter metal. That means a 20 kilogram thixome molded magnesium casting is roughly equivalent to a 30 kilogram aluminum casting. For reference, the rear casting on the Model Y is about 65 kilograms, and for the front casting it's closer to 80 kilograms. So if Idra can double or triple the injection pressure of their thixotropic piston injection units, a company like Tesla should be able to manufacture full underbody castings with their existing gigacasting machines.
此外,对于相同的注塑重量,镁可以制造更大的铸件,因为它是一种较轻的金属。这意味着一个20千克的凝胶模铸造镁铸件大约相当于一个30千克的铝铸件。以参考为依据,Model Y的后部铸件大约重65千克,前部铸件更接近80千克。因此,如果Idra能够将他们的琥珀糖体柱塞注射机的注射压力提高一倍或三倍,像特斯拉这样的公司应该能够使用他们现有的巨型铸造机制造完整的底盘铸件。
As a final note, with all the benefits of thixome molding, why is Idra focused on thixome molded magnesium instead of thixome molded aluminum? My guess is that it's because magnesium has more to gain from thixome molding than aluminum does, and that's for two reasons. First, as we saw earlier, thixome molding solves the cover gas problem for magnesium, whereas aluminum doesn't require a complex injection system to avoid contact with oxygen in the atmosphere because it's not as reactive.
最后一点,考虑到熔模成型的所有优点,为什么Idra将重点放在熔模成型的镁而非铝上呢?我猜测这是因为相比铝,镁在熔模成型方面有更多利益可得,原因有两个。首先,正如我们之前所见,熔模成型解决了镁气体覆盖问题,而铝并不需要一个复杂的喷射系统来避免与大气中的氧气接触,因为它的反应性较低。
Second, thixome molding gives the corrosive aluminum additional parts to corrode, which adds expense.
其次,这种翻铸工艺会增加腐蚀铝材的部件,从而增加了成本。
What do I mean by that? Let's start by looking at aluminum gigacasting as an example. The molten aluminum used for gigacasting is more corrosive to the steel dye than the semi-multen magnesium used in thixome molding. That's because the hotter the metal, the more reactive it becomes, and molten aluminum is much hotter than semi-multen magnesium. Additionally, even at similar temperatures, aluminum is more reactive with the dye than magnesium.
那是什么意思呢?让我们以铝合金大型浇铸作为例子来开始讨论。用于大型浇铸的熔化铝比凝固铸造中使用的半熔态镁对钢模具的腐蚀性更强。那是因为金属温度越高,其反应性越强,而熔化铝的温度比半熔态镁高得多。此外,即使在相似的温度下,铝与模具的反应性也比镁更高。
The result is that dyes for thixome molded magnesium last about two to three times as long as they do for aluminum gigacasting. While it is true that with aluminum thixome molding that the aluminum would be cooler than it is with gigacasting, it would still be hotter than magnesium because aluminum's melting temperature is slightly higher than magnesium's. Furthermore, as I said, even at similar temperatures, aluminum is more reactive with the steel dyes than magnesium.
结果是,用于鑄造镁合金的厚浆染料的使用寿命约为用于铝合金巨型鑄造的两到三倍。尽管对于铝合金的厚浆鑄造来说,铝的温度会比巨型鑄造时较低,但仍然会比镁高,因为铝的熔点稍高于镁。此外,正如我所说的,即使在相似温度下,铝与钢模具的反应性也比镁更高。
What all that means is thixome molded aluminum would chew through dyes more quickly than thixome molded magnesium, but it would also have a new part to react with. The expensive steel auger that's used to convey the semi-multen aluminum to the injection chamber. That means higher maintenance costs.
所有这些意味着,熔钢铝的模压会比熔镁的模压更快地损耗模具,但同时也会导致与新零件的反应。这种昂贵的钢螺旋输送器用于将半熔化的铝送入注塑腔室。这意味着维护成本更高。
With that in mind, in my view, it makes more sense to use thixome molding with magnesium. That's because compared to aluminum, thixome molded magnesium will offer lower maintenance costs due to longer dye and auger life and produce larger parts for the same shot weight, which should have equal or greater strength and ductility thanks to lower porosity. The only question is whether there's enough magnesium on the market at a low enough price to make thixome molded magnesium viable.
考虑到这一点,在我看来,使用镁合金进行压铸加工更有意义。这是因为与铝相比,经过压铸的镁合金将提供更低的维护成本,因为具有更长的模具和螺杆寿命,并且可以生产相同射重下更大的零件,这些零件应该具有相等或更高的强度和延性,这要归功于较低的孔隙度。唯一的问题是是否市场上有足够廉价的镁合金可用于使压铸加工的镁合金变得可行。
In short, as I'll cover later in the series, currently magnesium is expensive and scarce, but that will change as the decade progresses, so EDRA is positioning themselves well with their magnesium thixome molding gambit.
简而言之,正如我将在本系列中稍后介绍的那样,目前镁的价格昂贵且稀缺,但随着这个十年的进展,这种情况将会改变,因此EDRA在他们的镁等离子体成型策略中位置合适。
In summary, at a high level, thixome molded magnesium uses the same high pressure cold chamber die casting machines that gigacasting uses, but it requires an injection system that can generate high enough pressures to inject semi-multen magnesium into the dye chamber instead of fully molten aluminum.
总而言之,在高层次上,热浸淬模铸镁使用和大型铸型相同的高压冷室压铸机器,但需要一个能够产生足够高压力将半熔化镁注入模具室的注射系统,而不是完全熔化的铝。
So thixome molded magnesium is a more difficult engineering challenge than aluminum gigacasting, but it's worth it. By using magnesium instead of aluminum and semi-multen metal instead of fully molten metal, it dramatically improves the quality of the cast part by reducing porosity, which improves the strength and ductility of the magnesium part, while producing parts that are a third lighter.
这种使用半熔融金属制造的熔模镁材料比铝巨型铸造更具挑战性,但也是值得的。通过使用镁材料代替铝材料,并采用半熔融金属而不是完全熔融金属,可以显著提高铸件的质量,减少孔隙率,从而提高镁件的强度和延展性,同时使零件重量减轻三分之一。
The challenges with magnesium meant that up until a few years ago, the size of thixome molded magnesium parts were limited to less than 5 kilograms, and automotive use cases tend to require larger parts. However, that's changing with EDRA's new thixome molded piston injection units that can handle shot weights of up to 20 kilograms. And in my view, the same way that gigacasting machines are now almost two and a half times larger than the first machines that were introduced a few years ago will likely see EDRA offer much larger shot weights in the next few years for thixome molding.
镁合金的挑战意味着直到几年前,熔铸镁合金零件的尺寸仅限于不到5公斤,而汽车使用通常需要更大的零件。然而,EDRA公司的新型熔铸镁合金活塞喷射装置可以处理最多20公斤的喷射重量,这一情况正在发生改变。在我看来,就像目前的超大铸造机器已经是几年前推出的机器的两倍多一样,EDRA公司在未来几年很可能会提供更大的喷射重量用于熔铸镁合金。
So in the next video of the magnesium series, I'll go a level deeper to explore how thixome molded magnesium would affect the manufacturing and design of castings compared to aluminum gigacastings, where they could be used and their advantages.
在镁合金系列的下一个视频中,我将进一步探讨熔敬模铸造镁合金与铝型铸造的制造和设计的差别,讨论它们可以应用于哪些领域以及它们的优势。
If you enjoyed this video, please consider supporting the channel by using the links in the description. Also, consider following me on X. I often use X as a test bed for sharing ideas, and X subscribers like my Patreon supporters generally get access to my videos a week early.
如果您喜欢这个视频,请考虑通过描述中的链接支持本频道。另外,请考虑在X上关注我。我经常将X作为一个测试基地来分享想法,而像我的Patreon支持者一样,X的订阅者通常可以提前一周观看我的视频。
On that note, a special thanks to my YouTube members, X subscribers, and all the other patrons listed in the credits. I appreciate all of your support, and thanks for tuning in.
在此,我要特别感谢我的YouTube会员、X位订阅者以及所有列入致谢名单的赞助人。我非常感激你们的支持,谢谢你们的收看。