Tesla's Unboxed Process // A Closer Look
发布时间 2024-10-08 13:57:02 来源
摘要
Tesla devoted about 4 minutes to the unboxed process at Investor Day, so today I'm going to walk you through a closer look to ...
GPT-4正在为你翻译摘要中......
中英文字稿 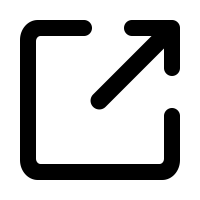
Welcome back everyone, I'm Jordan Geesigee and this is The Limiting Factor. A few months back, I did some surveys to see what topics people wanted me to make videos on. Tesla's unboxed process came in at the top of the list, which surprised me because Tesla gave a great presentation of the unboxed process at Investor Day. I didn't feel like there was much to add on the topic. However, when I reviewed the presentation, I found that the time dedicated to explaining the unboxed process was short, at only about 4 minutes long, and also glossed over some key points. So today, I'm going to expand on Tesla's presentation by showing how grossly inefficient and awkward the traditional vehicle manufacturing process is, why the unboxed process is such an improvement and provide more context on some of Tesla's key points.
欢迎回来,大家好,我是Jordan Geesigee,这里是The Limiting Factor。几个月前,我做了一些调查,看看大家希望我制作哪些主题的视频。令我惊讶的是,特斯拉的“无盒”工艺在列表中名列前茅,因为特斯拉在其投资者日的演讲中已经很好地展示了这一工艺。我当时觉得没什么可再补充的。然而,当我回顾那次演讲时,我发现用于解释“无盒”工艺的时间很短,仅有4分钟左右,且遗漏了一些关键点。所以今天,我将扩展特斯拉的演讲内容,展示传统汽车制造工艺有多么低效和繁琐,为什么“无盒”工艺是一个巨大的进步,并为特斯拉的一些关键点提供更多背景信息。
Before we begin, a special thanks to my Patreon supporters, YouTube members and Twitter subscribers, as well as RebellionAir.com. They specialize in helping investors manage concentrated positions. RebellionAir can help with covered calls, risk management, and creating a money master plan from your financial first principles. In the Investor Day presentation on the unboxed process, Tesla started by using this flow chart to show the four stages of a traditional vehicle manufacturing process, which are stamping, building the body, painting, and then final assembly. Those four stages are parts of one continuous manufacturing line. So whenever and wherever an issue occurs, it blocks almost all production upstream of that point. I say almost all because some production may still occur because there's some buffering capacity between the stages. This is important and we'll come back to it later in the video.
在开始之前,特别感谢我的Patreon支持者、YouTube会员和Twitter订阅者,以及RebellionAir.com。他们专注于帮助投资者管理集中持仓。RebellionAir可以帮助处理备兑看涨期权、风险管理,并根据你的财务基本原则制定资金管理计划。在投资者日的展示中,特斯拉用这个流程图展示了传统车辆制造过程的四个阶段:冲压、车身建造、喷漆和最终组装。这四个阶段是一个连续生产线的一部分。因此,无论何时何地发生问题,几乎都会阻碍该点上游的所有生产。我说“几乎全部”是因为在这几个阶段之间有一些缓冲能力,可能仍会进行一些生产。这一点很重要,稍后我们在视频中会再讨论。
Tesla then showed an animation of the traditional vehicle manufacturing process and explained that in the body shop, stamped panels are put in a framing station to assemble the frame of the vehicle. This forms the box that Tesla is doing away with in their unboxed process. Then the doors are mounted and the entire vehicle is painted. After that, bizarrely, the doors are taken back off so they can be finished separately, and so that the interior of the vehicle can be assembled through the openings in the vehicle frame. That's an awkward process because people have to enter and exit the vehicle frame to assemble it, and when it comes to assembling the underside of the vehicle, that massive frame has to be lifted to provide access. Then the vehicle has to be lowered again. The seats are put in the car, the glass mounted, and then the finished doors finally return to be remounted.
特斯拉随后展示了一段关于传统汽车制造流程的动画,解释了在车身车间中,冲压板件会被放到一个框架站,用来组装车辆的框架。这就形成了特斯拉在其“无框架”流程中所摒弃的箱体结构。然后安装车门,并为整个车辆喷漆。之后,奇怪的是,车门会被移除,以便单独加工,并且便于通过框架的开口来组装车辆内部。这个过程有些麻烦,因为工人需要进出车架进行组装,特别是在组装汽车底部时,必须将整个大框架抬起以便操作,随后再将车辆降下。接着,安装座椅、玻璃,最后加工完毕的车门再次被装回。
The end result of the unboxed process is that there's a lot of time, movement, and equipment that's unnecessary. In fact, the animation Tesla showed didn't quite do justice to the inefficiency of a traditional process because it was greatly accelerated and simplified to keep their presentation brief and punchy. With that in mind, let's take a closer look at the inefficiencies and pain points of a traditional vehicle manufacturing process. First, on screen is a video of a framing station. Framing stations like this are used to assemble the body of the vehicle. Assembling the body is an awkward task because thin stamped metal tends to be flimsy and rebounds to a certain degree when stamped. And of course, because the vehicle frame forms part of the core of the vehicle, if it's not millimeter precise, the rest of the vehicle doesn't come together correctly. The next pain point with a traditional vehicle manufacturing process is coating and painting. With a boxed process, most or all of the vehicle is coated or painted because it's effectively one giant part. It's also awkward. For example, with immersion coating, the nooks and crannies of the frame can lead to air pockets where the coating doesn't happen or where the liquid can pool, so it has to be rotated through the pool of chemicals.
在传统制造过程中,最终结果就是很多时间、动作和设备都是不必要的。事实上,特斯拉展示的动画并没有完全体现出传统工艺的低效,因为它经过了极大加速和简化,以使他们的演示简洁有力。考虑到这一点,让我们仔细看看传统汽车制造过程中的低效和痛点。首先,屏幕上展示的是一个车架组装站的视频。像这样的车架组装站用于组装车辆的车身。组装车身是一项麻烦的任务,因为薄薄的冲压金属往往很脆弱,并且在冲压后会有一定程度的回弹。而由于车辆车架是车辆的核心部分之一,如果它不精确到毫米,那么车辆的其他部分就无法正确组装。
传统汽车制造过程中的下一个痛点是涂层和喷漆。在封闭加工流程中,整个或大部分车辆都会被涂层或喷漆,因为它实际上是一个巨大的整体部件。这也很麻烦。例如,在浸泡涂层中,车架的角落和缝隙可能会形成气泡,导致涂层不完全,或者液体可能会汇集,所以车架必须在化学池中旋转以确保涂层均匀。
Third, as Tesla pointed out, the doors are mounted before painting, which is time consuming. Then after painting, they're removed and have to travel to another line to be fitted out with parts like wiring and trim before being returned and remounted to the vehicle. That means redundant operations, extra travel, and the redundant machinery necessary to move the doors around, mount them, unmount them, and then remount them.
第三,正如特斯拉指出的那样,车门是在喷漆之前安装的,这个过程非常耗时。喷漆之后,车门会被拆卸下来,并送到另一条生产线上进行配件安装,比如电线和内饰。然后,再把这些车门返回并重新装到车上。这就意味着重复的操作、额外的运输,以及为移动车门、安装和拆卸车门所需的额外设备。
Fourth, the animation from Tesla showed the interior dropping in somewhat magically, but that's not reality. Everything in the vehicle has to be shoehorned in with large robots, or humans have to enter and exit the vehicle to mount every part, which is slow and physically taxing because it involves a lot of bending, twisting, and craning of the neck. Fifth, in the Investor Day presentation, Tesla pointed out that with a traditional vehicle manufacturing line, the vehicle frame has to be lifted in some parts of the assembly process to provide access for workers. Some manufacturers do tilt the vehicle to reduce worker fatigue, but as we'll soon see, where humans are used, the unboxed process should, fundamentally, result in less strain and fatigue.
第四,特斯拉的动画展示中,内饰似乎是魔法般掉落到位,但这并不现实。车辆中的所有部件都必须用大型机器人精准安装,或者由工人进入和走出车辆来安装每个部件。这一过程既缓慢又费力,因为需要大量的弯腰、扭动和抬头。第五,在投资者日的演示中,特斯拉指出,在传统的汽车制造生产线上,车辆框架在装配过程中需要被抬起,以便工人操作。一些制造商会倾斜车辆来减少工人的疲劳,但正如我们将要看到的,使用人力的情况下,"无框化"流程从根本上应该可以减少应力和疲劳。
Moving along, Tesla's next point at Investor Day was that Tesla has already started implementing the unboxed process to a small degree with the Model Y. The structural battery pack, motors, chassis, and seats of the vehicle, or skateboard, are built as a subassembly on a parallel manufacturing line, and then joined to the upper structure of the vehicle on the main assembly line. That reduced the length of the final assembly line by 10%. On that note, I've heard a number of people say that the unboxed process isn't possible, or that Tesla will fail, but what this video shows is that Tesla has already been using a partially unboxed process for at least a couple of years now. It is, of course, another thing entirely to make a vehicle using a fully unboxed process, but it's clearly Tesla's end goal, and they've been working towards that goal incrementally and with success.
继续前进,特斯拉在投资者日上提到的下一个重点是,特斯拉已经在Model Y上小范围地开始实施无框架工艺。车辆的结构电池组、电机、底盘和座椅等,都在一条平行的生产线上作为一个子组件组装,随后与车辆的上部结构在总装线上结合。这样缩短了最终装配线的长度10%。关于这一点,我听到一些人说无框架工艺不可行,或者特斯拉会失败,但这段视频显示,特斯拉至少在最近几年来一直在使用部分无框架工艺。当然,完全采用无框架工艺制造车辆是一件完全不同的事情,但显然这是特斯拉的最终目标,他们一直在逐步实现这一目标并取得了成功。
So with that trajectory in mind, I'm expecting that at a minimum, the process used to create their upcoming vehicles will become increasingly unboxed, which in my view means a greater number of parallel production lines and fewer redundant operations. We'll come back to that point in a moment. Next, Tesla explained at a first principles level why it was more efficient to produce the skateboard of the Model Y on a parallel production line or unboxed process. Running in and around a 5 meter long and 1.5 meter tall box creates a lot of inefficiencies. That's because it basically becomes a jungle gym for the workers when they're moving and mounting parts in and around the vehicle.
考虑到这样的发展趋势,我预计至少他们在制造即将推出的车辆时会采用越来越多的“无盒化”流程。在我看来,这意味着将会有更多的平行生产线和更少的重复操作。我们稍后会回到这一点。接下来,特斯拉从基础原理的角度解释了为什么在平行生产线或无盒化流程中生产Model Y的底盘更高效。在一个大约5米长、1.5米高的盒子里进行作业会造成很多效率低下的问题。这是因为工人在移动和安装车辆周围的零件时,整个环境就像一个“攀爬架”,影响工作效率。
By breaking the vehicle down into smaller parts or subassemblies, it creates better spacetime efficiency. In my view, in English, that means four things. First, the workers and robots will have free access to every aspect of the subassemblies, with no physical obstacles. Second, the workers and robots won't have to move as far to access any part of each subassembly. Third, the workers will experience less fatigue because they no longer have to bend, twist, crawl, or crane their necks like they do with a traditional manufacturing process. The subassemblies can be on mobile carts that can be height adjusted to the optimal working height, which will increase speed and reduce strain. Fourth, it may be easier to design and program the robots to work on the subassemblies because all the motions will be more direct and linear.
通过将车辆分解成更小的零部件或子装配,这种方法可以提高时空效率。在我看来,用简单的中文表达,这意味着四点:首先,工人和机器人可以自由地接触每个子装配的各个方面,没有物理障碍。其次,工人和机器人不需要走太远就能接触到每个子装配的任何部分。第三,工人不再需要像传统制造过程那样弯腰、扭动、爬行或伸长脖子,从而减少疲劳。子装配可以放在可移动且高度可调节的推车上,以达到最佳工作高度,从而提高速度并减少压力。第四,设计和编程机器人来处理子装配可能更容易,因为所有运动都会更直接和线性。
Fifth, because the six different subassemblies are being worked on at the same time rather than sequentially, it's going to accelerate the speed that the vehicle is manufactured. Overall, Tesla says the unboxed process will increase efficiency or speed by 30%, and increase the number of workers or robots for a unit of factory space by 44%, which means a smaller factory. Before we move on, in my view, the simplest way to think about the unboxed process is that by moving from a large box to multiple subassemblies, you're increasing the actionable surface area, which naturally accelerates the speed that actions can take place. This is much the same way that a chemical reaction can be accelerated by using powder rather than a block of material.
第五,由于六个不同的子组件是同时进行而不是顺序进行的,这将加快车辆的制造速度。特斯拉表示,整体而言,无盒(unboxed)流程将提高30%的效率或速度,并增加44%每单位工厂空间的工人或机器人的数量,这意味着工厂可以更小。在我看来,理解无盒流程的最简单方法是,通过从一个大箱子转到多个子组件,增加了可操作的表面积,自然就加快了操作进行的速度。这就像用粉末而不是块状材料来加速化学反应一样。
Next, Tesla goes on to say that the end result of breaking the vehicle down into subassemblies is that the flow chart for the production line would go from a linear process flow to a parallel process flow. What are the implications of that? As I said at the beginning of the video, in a traditional vehicle manufacturing line, if anything goes wrong in any of the four manufacturing stages, the whole manufacturing line ends up blocked. That means the manufacturing line can only move as fast as the slowest part of the line. But it's also important to note that, as I said earlier, wherever a slowdown or blockage occurs, buffering can occur further upstream.
接下来,特斯拉提到,将车辆分解为子装配件的最终结果是,生产线的流程图将从线性流程变为并行流程。这种变化有什么影响呢?正如我在视频开头所说的,在传统的汽车生产线上,如果四个生产阶段中的任何一个出现问题,整个生产线就会被阻碍。这意味着生产线的速度只能与最慢的部分一致。但同样需要注意的是,正如我前面提到的,无论在哪里发生速度减慢或阻塞,进一步向上游的缓冲都会出现。
That is, partially finished vehicles or parts can build up at the end of each manufacturing stage. The overall line is still rate limited by the blockage or slowdown, but the buffering can provide a smoothing effect so that the production can resume more quickly. How would a parallel or unboxed production process handle slowdowns and blockages? Given that we don't know exactly how Tesla is implementing the unboxed process, bear with me while I speculate. When we look at the parallel manufacturing flow chart, my assumption is that most of the manufacturing burden in terms of robot or man hours is actually going to be offloaded to the parallel processes.
也就是说,每个制造阶段结束时,未完成的车辆或零件可能会堆积。整个生产线还是会因为阻塞或减速而受到限制,但这种缓冲可以起到平滑作用,使生产能够更快恢复。如果采用平行或无盒(unboxed)生产流程,如何应对减速或阻塞呢?鉴于我们并不确切了解特斯拉是如何实施无盒流程的,请容我进行一些推测。查看平行生产流程图时,我的假设是,大部分在机器人或人工工时方面的制造负担实际上会转移到平行流程中进行。
Why? Because that's where most of the thousands of wires, hoses, and mechanical linkages will be fitted together. Then, when it comes to the vehicle assembly process, it's mostly a matter of bolting, plugging, and gluing the six major sub-assemblies to each other. If that's the case, bottlenecks at the assembly stage would be much less likely, and the limiting factor for production speed would be pushed upstream to the parallel sub-assembly lines, which means when there is a production issue, it's localized to a specific production area rather than blocking the entire factory. Yes, that means the rest of the sub-assembly lines would then start buffering production.
为什么?因为大多数成千上万的电线、软管和机械连接件都将在那里组装在一起。然后,在车辆组装过程中,主要就是将六个主要子组件互相用螺栓固定、插接和粘合。如果是这样的话,装配阶段出现瓶颈的可能性就会小很多,生产速度的限制因素会被推到上游的平行子装配线。这意味着当出现生产问题时,它只会局限于某个特定的生产区域,而不会影响整个工厂。是的,这也意味着其余的子装配线将开始缓冲生产。
However, given that there would be many parallel production lines producing relatively small sub-assemblies, when buffering does occur, the sub-assemblies wouldn't take up as much space as partially finished vehicles. That means more instances of buffering across the vehicle factory and a greater number of parts in each buffer. We've seen this with gigacastings where Tesla can stockpile a huge number of castings during production ramps, because the casting process sometimes ramps faster than the rest of the line. I'm not sure what those employees then do, but I suspect they spend more time refining the efficiency of their part of the production process, go help in other areas of the factory, or reduce their work hours. If the same were true in the unboxed process, if the sub-assembly lines that are running faster than the other lines build a large enough buffer, those employees may be able to lend a hand on the slower assembly lines. What all this means is that the unboxed process should not only accelerate the production rate of each part of the vehicle, it may also smooth and therefore accelerate the overall manufacturing flows through the factory.
然而,考虑到有许多平行的生产线在制造相对小的子组件,当出现缓冲时,这些子组件不会占用像部分完工车辆那么多的空间。这意味着整个汽车工厂中会有更多缓冲区实例,每个缓冲区内的零件数量增多。我们在特斯拉的巨型铸件生产中已经看到这一点,因为铸造的产量有时会比生产线的其他部分更快地提升,所以可以在生产增量期间储存大量铸件。我不确定那时这些员工会做什么,但我猜他们可能会花更多时间提高他们在生产过程中负责部分的效率,去工厂的其他区域帮忙,或者减少工作时间。如果在“去盒化”流程中也是如此,那么那些运行速度比其他流程更快的子组件生产线如果建立了足够大的缓冲区,那些员工可能会去帮助较慢的装配线。这一切意味着,“去盒化”流程不仅应该加快每个车辆部件的生产速度,还可能理顺并因此加速工厂内整体的制造流程。
The last part of Tesla's presentation on the unboxed process was this animation. It shows that only the parts that need paint get painted, and that the six different sub-assemblies are manufactured separately. Then, the sub-assemblies come together fully tested and only once on the vehicle assembly line. There, the front and rear of the vehicle, the sides of the vehicle, and the structural battery pack with seats bolt together like Legos before the doors, glass, and wheels are mounted to finish the vehicle. Notably, at this point in the presentation, Tesla also pointed out that they're already using a similar process with the Cybertruck. That reinforces the point that Tesla's been working towards the unboxed process for years, and that to a limited degree, it's already been implemented and trialed in vehicles that are on the road today. It's just that for Tesla's next generation vehicles, their goal is to take the final leap and use a fully parallel or unboxed process.
特斯拉关于无盒化流程的演示最后部分展示了一个动画。动画显示,只有需要喷漆的零件才会被涂上颜色,六个不同的子组件分别制造。然后,这些子组件在车辆装配线上组合在一起,并经过完全测试。在装配线上,车辆的前后部分、侧面和带座椅的结构电池包像乐高积木一样拼接在一起,然后安装车门、玻璃和车轮,完成整车组装。特别值得注意的是,在演示中,特斯拉还指出他们已经在Cybertruck上使用了类似的流程。这就证明了特斯拉多年来一直在努力推进无盒化流程,并且在一定程度上,这种流程已经在现有的路上车辆中得到实施和试验。对于特斯拉下一代车辆,他们的目标是最终实现全面的并行或无盒化流程。
Earlier, I walked you through the pain points of a traditional vehicle manufacturing process. Let's look at how each of those pain points is resolved or reduced with the unboxed process. First, although the unboxed process will still use stamped parts for things like the doors and body panels, the stampings are reduced by about two-thirds thanks to the gigacastings in the front and rear underbodies. That's something Tesla's been doing for a couple of years already, but with the unboxed process they'll take it to the next level. The core of the vehicle will be castings and the structural battery pack, and the sides will just bolt on to tie everything together. So, framing stations will no longer be needed.
早些时候,我向你介绍了传统汽车制造过程中的一些痛点。现在,我们来看看这些痛点是如何通过"拆箱"流程得到解决或缓解的。首先,虽然"拆箱"流程仍会使用冲压件来制造车门和车身面板等部件,但由于前后底盘使用了大型铸件,冲压件的用量减少了约三分之二。特斯拉已经在这方面耕耘了几年,而通过"拆箱"流程,他们将更进一步。车辆的核心将由铸件和结构电池包组成,车身两侧会直接螺栓连接,从而将所有部件整合在一起。因此,不再需要装配框架的车间了。
Second, the unboxed process eliminates unnecessary coating and painting. For example, the entire car doesn't have to be immersion coated, so individual parts can be coated as needed. And for painting, they can be run through the paint shop in racks that may allow for more efficient painting suites. It'll also reduce energy usage for drying and baking steps. Just because more of the space in the paint shop will be filled with parts that must be painted rather than heating empty air space and parts that may not actually need to be painted.
其次,无包装工艺消除了不必要的涂覆和喷漆。例如,整辆车无需进行浸涂,可以根据需要对各个零件进行涂覆。对于喷漆,这些零件可以通过在喷漆车间的货架上进行处理,从而实现更高效的喷漆作业。这一过程还将减少烘干和烘烤步骤的能耗。因为在喷漆车间中,会有更多必须喷漆的零件填满空间,而不是加热那些不需要喷漆的空隙和零件。
Third, with the unboxed process, the doors are fully assembled before being attached to the vehicle, so the mounting operation occurs just once. Fourth, with the unboxed process, workers no longer need to enter and exit the vehicle to install the interior. And there's no bulky parts like seats or the dash that have to be shoehorned in through the door openings. Fifth, although the vehicle will still likely be raised and lowered with the unboxed process, to mount the battery pack and seats, most of the assembly operations will likely occur on carts at a comfortable height. That means less workers strain working underneath vehicles. The end result of the benefits of the unboxed process is that Tesla estimates that the factory footprint will be reduced by 40%, which will allow them to build factories faster, with less capex and greater output per unit of floor space.
第三,在无盒化流程中,车门在安装到车辆上之前就已经完全组装好了,所以只需进行一次安装操作。第四,采用无盒化流程后,工人不再需要进出车辆来安装内部配件,并且不需要通过车门缝隙费力安装像座椅或仪表板这样的大件。第五,虽然在无盒化流程中,车辆仍可能需要升降以安装电池组和座椅,但大部分组装操作可能会在舒适高度的推车上进行。这意味着工人在车辆底部工作时会减少身体的劳损。无盒化流程的最终好处是,特斯拉预计工厂占地面积将减少40%,这将使他们能够更快地建造工厂,减少资本支出,并提高每单位地面面积的产出。
Tesla also pointed to a 50% reduction in cost of goods sold, but that's for a smaller, next generation vehicle. On a like for like basis, the manufacturing cost savings from the unboxed process appears to be around 13.5%. In summary, the unboxed process is expected to accelerate assembly speed. May smooth and accelerate the production rate of the factory as a whole will eliminate redundant process steps and the machinery required for those process steps and reduce the size of the factory, which all leads to lower production costs. Relative to the other innovations that Tesla's tackled in the past, I view the unboxed process as a lower risk.
特斯拉还指出,下一代小型车辆的销售成本降低了50%。但就类似车型而言,通过“无盒化”流程的制造成本节约约为13.5%。总的来说,“无盒化”流程预计将加快装配速度,有可能使整个工厂的生产速度更快更顺畅,消除多余的工序步骤和相应的设备,缩小工厂规模,从而降低生产成本。相对于特斯拉过去处理的其他创新,我认为“无盒化”流程的风险较低。
Real risky and difficult, but not a moonshot. That's because, as I pointed out in my last video, Tesla's been laying the groundwork for the unboxed process for well over a decade. So a lot of the technologically difficult problems appear to be already solved. With those technologies in place, it should actually be easier and faster to produce vehicles with the unboxed process. Not only that, besides having the basic technology toolkit in place to do the unboxed process, Tesla's already, to a limited degree, used the unboxed process and the model Y and to a greater extent the Cybertruck.
这很冒险和困难,但不是异想天开。这是因为,如我在上一个视频中所指出的那样,特斯拉已经为无盒流程铺垫了十多年。因此,许多技术上的困难问题似乎已经解决。有了这些技术,就应该更容易、更快速地通过无盒流程生产车辆。不仅如此,除了拥有实施无盒流程的基本技术工具包,特斯拉已经在一定程度上在Model Y中使用了无盒流程,并在Cybertruck中应用得更多。
I suspect that's because the Cybertruck doors don't need to be painted so are mounted only once, because the battery pack and seat sub assembly now appears to be a separate sub assembly from the front and rear that contain the motors and chassis, and because the Cybertruck should be much more easily broken down into sub assemblies because it uses Tesla's Etherloop wiring architecture, which allows for plug and play connectivity between the sub assemblies rather than requiring a hardware connection to a main CAN bus cable.
我猜这是因为Cybertruck的车门不需要喷漆,所以它们只需要安装一次。同时,电池组和座椅的子装配现在似乎是一项独立的子装配,与包含电动机和底盘的前后部分分开。此外,Cybertruck应该更容易分解成多个子装配,因为它使用了特斯拉的Etherloop布线架构,这使得各个子装配之间可以通过即插即用的方式连接,而不需要通过主CAN总线电缆进行硬件连接。
What all this means is that Tesla has done a lot to de-risk the fully unboxed process that's expected to be used in their next generation vehicles. The only question that remains for me is how pure of an implementation of the unboxed process Tesla will be able to achieve for those vehicles, and we should get more insights on that in the next year as Tesla expands production in their existing facilities and breaks ground in new locations. If you enjoyed this video, please consider supporting the channel by using the links in the description. Also consider following me on X. I often use X as a test bed for sharing ideas, and X subscribers like my Patreon supporters generally get access to my videos a week early.
这段话的意思是,特斯拉在降低全新生产工艺风险方面做了很多努力,这一工艺预计将用于他们的下一代汽车。唯一的问题是,特斯拉能够在多大程度上实现这一工艺的纯粹运用。随着特斯拉在现有工厂扩大生产并在新地点开工建设,我们将在明年获得更多洞见。如果你喜欢这个视频,请考虑通过描述中的链接支持该频道。另外,欢迎在X平台上关注我。我经常使用X作为分享想法的测试平台,X的订阅者和我的Patreon支持者通常能比其他人提前一周看到我的视频。
On that note, a special thanks to my YouTube members, X subscribers, and all the other patrons listed in the credits. I appreciate all of your support, and thanks for tuning in.
借此机会,特别感谢我的 YouTube 会员,X 订阅者,以及所有其他在片尾鸣谢中的支持者。感谢你们的支持,也谢谢你们的收看。